5 Elements of Circular Exhibition Development
Explore ways to reduce waste and increase the environmental sustainability of museum and gallery exhibitions and theatre staged environments.
What are the 5 Elements?
The 5 key elements of exhibition development include: Planning, Designing, Materials choices, Building and Unbuilding (i.e. de-constructing or disassembling at the end of exhibitions).
SAGE invites you to move beyond waste management and recycling practices to adopt circular solutions. The following sections provide tips and examples of circular practices in each of the five key elements (or stages) in the development of exhibitions and other staged environments.
Development of circular exhibitions and other staged environments refers to planning, designing and choosing materials that will avoid or reduce waste in the short- and long-term. It also includes ways to build and unbuild your staged environments to optimize materials use and avoid generating waste. This circular approach to exhibition development is more environmentally sustainable and may result in other benefits such as greater innovation, increased efficiencies and reduced costs.
The aim of this toolkit is to provide inspirational ideas and examples, and practical guidance for implementing a circular approach to choosing and using (and reusing) the materials required for exhibitions and staged events.
A circular approach to exhibition planning and development aligns with the principles of circularity, often referred to as the circular economy. In this system, materials are continuously reused and repurposed, preventing them from becoming waste.
Circular economy emphasizes environmental sustainability as well as economic efficiency through elimination of waste and extending the useful life of products and materials.
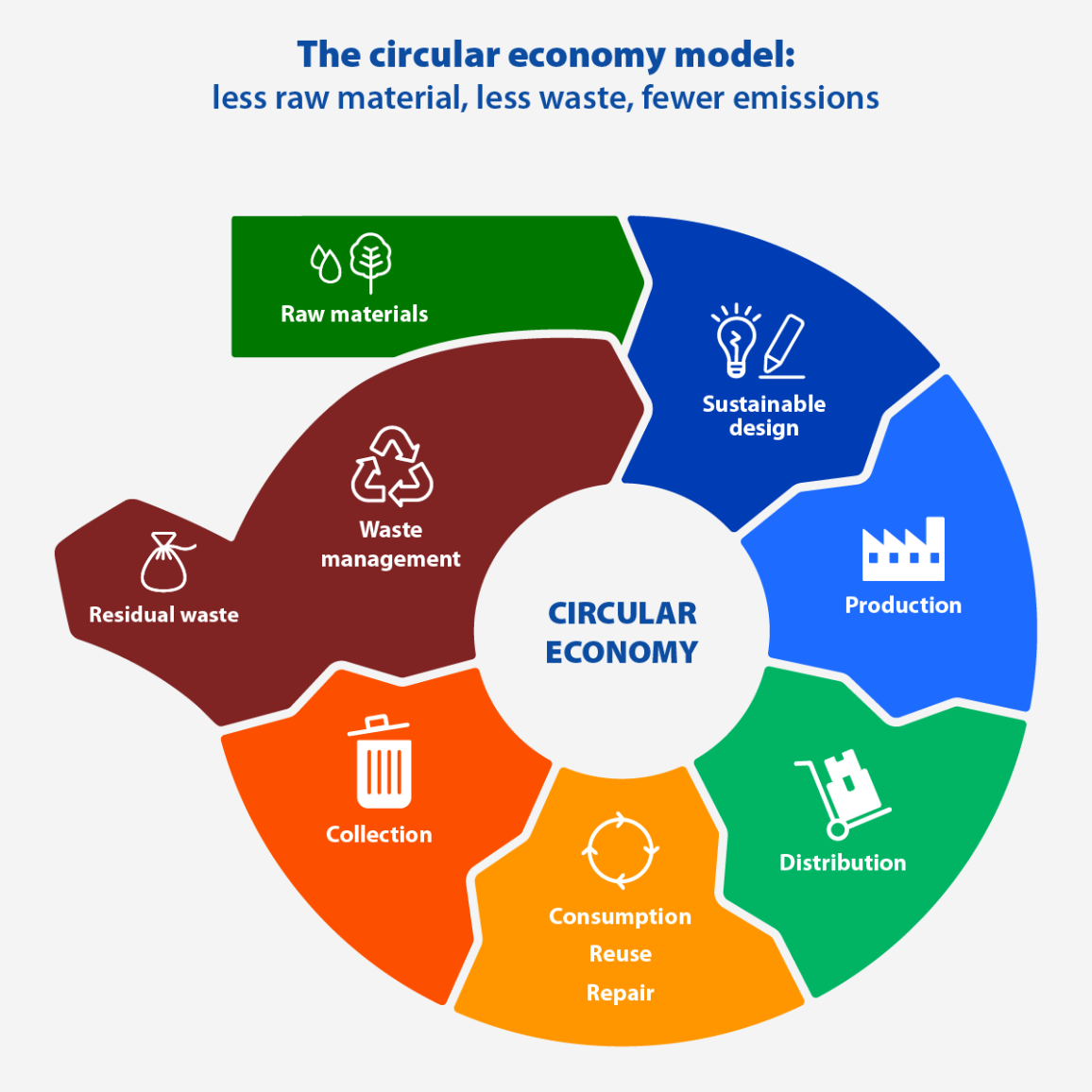
Circular practices involve carefully planning and implementing processes that minimize waste, preserve resources, and extend the life of materials and products. This approach emphasizes choosing materials that can be reused, refurbished, or recycled into new products, or composted. By extending the life of materials in circulation or repurposing or regenerating them for reuse, organizations avoid waste and associated greenhouse gas emissions.
There are many opportunities for museums, galleries, and theatres to establish policies and practices in pursuit of circular exhibition development. This SAGE Toolkit offers foundational guidelines and tips for circular practices, and we encourage you to use your own creativity and innovation to introduce or extend circularity into your exhibitions and staged environments.
Circular exhibition development requires thoughtfully building or assembling exhibitions to maximize materials use and avoid generating waste cut-offs and scrap materials. It also requires techniques for disassembling (unbuilding) exhibitions and staged environments to avoid and minimize waste at the end of the life of each project.
These 5 elements work together. Planning and design for circularity leads to choice of materials that are more durable and reusable, and to construction (building) and disassembly (unbuilding) practices that reflect circular decisions made in the planning and design stages.
Visit each of the 5 elements for quick tips, examples and more detailed discussion of circular exhibition development.
For other environmental considerations for museums, galleries, and theatres see the Resources & Inspiration section for other toolkits and guidance and the Creative Green Tools for measuring greenhouse gas emissions generated by your buildings and operations and your exhibitions and theatre productions.
Planning sets the stage for successful circular outcomes in exhibitions and other staged environments. Integrating circular economy principles into planning requires thinking beyond the next exhibition or theatre set to consider past and future staged environments. Key to circularity in this sector of the arts is designing, building and unbuilding exhibitions and theatre sets to eliminate (or greatly reduce) waste by keeping materials, products and props in circulation for as long as possible in order to extend their life. This must start at the planning stage to inform and guide all subsequent activities.
We’ve all heard of the 3Rs: reduce, reuse, recycle. Reuse within your own organization is one way to keep materials in circulation, but a circular economy considers other “Rs” as well. When planning staged environments consider these 5Rs before any design or construction of exhibitions or theatre sets begins.
The 5 Rs of Circularity
Step back and think about the theatre set or exhibition you want to create and ways you can do it without generating waste.
Before you buy new materials and props – review what is available in your inventory, or in your arts community to borrow or purchase used? What materials will be available upon disassembly of existing exhibits or theatre sets? If a material is not durable, are there alternatives that enable design and building for extended material life? Minimize use of materials that can only be used once.
Like refuse – can you avoid buying any (or as much) new materials for your next exhibition or theatre set? Can you avoid using non-durable or non-recyclable materials and goods in your theatre sets or museum exhibitions? Can you design and build in a way that minimizes or eliminates waste?
This is a critical planning element. It is an opportunity to leverage designers’ creativity to reuse materials from your own organization (or beyond), to look for ways to deploy used materials without compromising your production quality and impact. It is also important to inform the team to unbuild or disassemble the present exhibition or theatre set to preserve materials for reuse in your upcoming or further exhibitions.
At the planning stage rethink the life of the materials beyond this next project. Challenge your designers and fabricators to find ways to extend the life of the materials. Even if you don’t have an immediate need for the materials, extend their life by communicating and collaborating with other members of your community to share materials and props, to borrow, sell, or giveaway materials at the end of your exhibitions or productions.
Definition Staged Environments
Any carefully designed or constructed setting that is intended to support a specific experience, narrative, or purpose.
In the context of SAGE activities, it encompasses exhibitions in museums, galleries and science centres as well as theatre sets, as both are designed spaces meant to engage an audience or convey a message.This term is used throughout the SAGE toolkit.
Definition Circular Economy
An economic system based on the reuse and regeneration of materials or products, especially as a means of continuing production in an environmentally sustainable way. Circular economy emphasizes environmental sustainability and economic efficiency by eliminating waste and extending the useful life of products and materials.
A system in which materials are continuously reused and repurposed, preventing them from becoming waste. Circular economy practices involve carefully planning and implementing processes that minimize waste, preserve resources, and extend the life of materials and products. This approach emphasizes selecting materials that can be reused, refurbished, recycled into new products, or composted.
By extending the life of materials in circulation or repurposing or regenerating them for reuse, organizations avoid waste and associated greenhouse gas emissions. See Circularity in the 5 Elements for further info.
Quick Tips
Here are quick tips summarizing how to plan circular exhibitions and other staged environments. Visit How to plan circular exhibitions for more details.
Communicate, Engage & Specify. How?
- Bring the team together (internal and external service providers) to introduce circularity goals at the project kick-off – be as specific as possible and invite ideas.
- Start and end with the Project Pledge. Commit to relevant circular options listed in the Pledge; Review your Pledge in your project debrief.
- For external design or fabrication service providers, include contract language specifying low-waste design and circular practices. Be as specific as possible to guide the contractors.
- Review your inventory of materials before purchasing, and seek sources of used materials and props.
- Continue to engage the team on circularity ideas, challenges and solutions throughout project planning and development.
- For internal design and/or fabrication teams, create a culture of circularity with guidance on how to achieve low-waste and extend materials life.
- Share your commitment to circularity with your audience.
Manage Time and Budgets. How?
- Ensure you include lead time in the planning and design process to engage parties in your circularity goals.
- Make sure that building and unbuilding are not rushed as this often leads to assembly/disassembly methods that limit the potential for material reuse.
- Budgets for circularity include upfront meetings with the whole team, and may include purchases for materials and modular systems that last longer than one exhibition or theatre set.
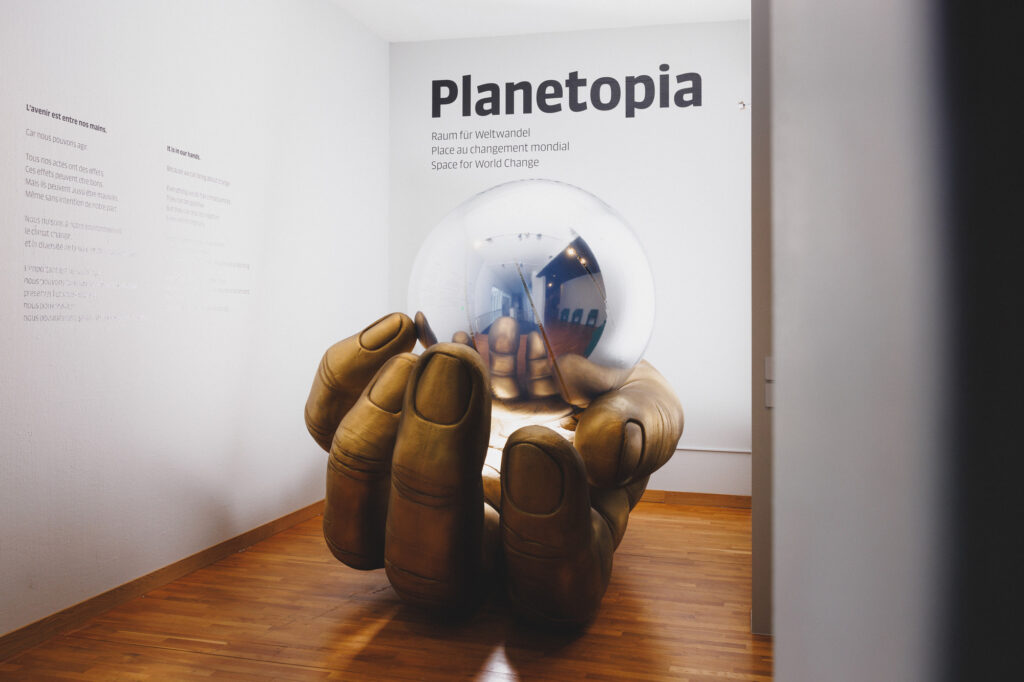
How To Plan Circular Exhibitions and Other Staged Environments
Thoughtful integration of circularity does not detract from the visitor experience or other goals of an exhibition or theatre event, but adding circular and sustainability goals is urgently needed in the art sector.
Introduce your circularity goals at the project kick-off. The linear process of handing off planning to designers and designers to builders can create problems, so ideally, bring all the key project contributors (staff and contractors) together to share your vision and include your circularity goals upfront before design or purchasing commences.
You may find the Circular Buy-In and Ideas Capture worksheets helpful. Use the Buy-in worksheet to guide conversations with your team to gain buy-in and encourage their ideas for how to achieve circular outcomes for the project. Use the Ideas Capture worksheet to re-think the exhibition or theatre set development process to integrate the 5Rs. Find these and other worksheets in the Circular Design Guide in the Resources & Inspiration.
If you’ve committed to a Project Pledge, review it with the team. While you may have high level circularity goals, ideas about how to execute them may come from the designer or fabricators or other members of the team. So, if you need to introduce or explain any of the 5Rs of circularity, take this opportunity to educate team members so you are all on the same page.
Continue to share your circularity commitments, ideas and constraints or challenges as you plan. If you have specific circularity goals (e.g. all lumber will be sourced from past projects) be sure to consider them now and convey those goals to the team. Challenge the team to re-think ways to achieve your exhibition or theatre set production goals to reduce waste, reuse materials, and enable future reuse (more on this is the Design and Building elements).
Include your circularity goals and specifications in development of the concept and schematic plans upfront before design or purchasing commences.
Explore high level curatorial and design opportunities for circularity, and explain how you aim to integrate circularity throughout the design, building and unbuilding phases, and invite ideas (and any concerns).
Commitment to circularity and lower greenhouse gas emissions should not be restricted to environment- or climate-themed productions.
Check-in that circular goals and specifications are not forgotten as planning and design progress. Also consider the end of the life of the staged environment – will it be in 4 months or 4 years? What materials will become available to recirculate? That is, do you plan to reuse some materials in future exhibitions or theatre sets? If not, plan to lend, sell or give away materials and props, and include these reuse considerations in the logistics and timelines for disassembly.
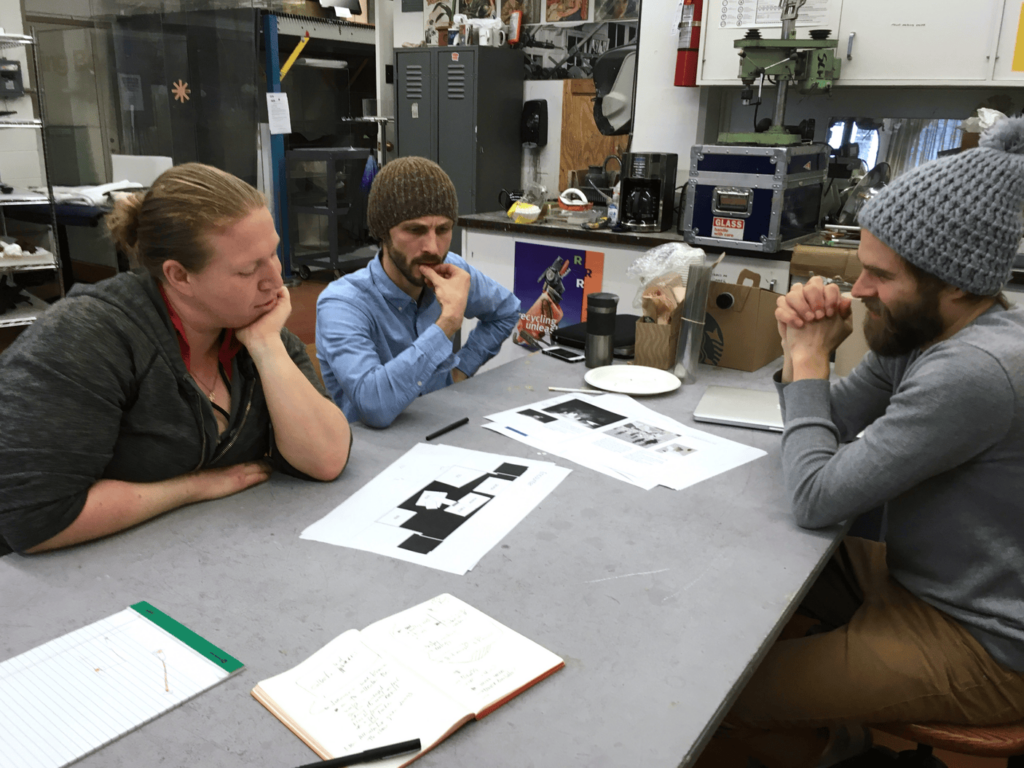
The National Theatre Museum in Wales set ambitious goals for greenhouse gas emissions, so that waste and other environmental impacts are rigorously evaluated before decisions are made about production and programming as well as other areas of the theatre’s operations. Looking to put your plans in writing for review, use this toolkit to guide you, and documents such as the SAGE Project Pledge, the SAGE Checklist and the template contract language may be helpful to guide planning.
Build an inventory of your materials or props. What’s in storage and what will become available upon disassembly of an existing exhibition? Keep this inventory up-to-date and consult it in the Planning stage to avoid unnecessary purchase of new materials.
When you do not have short-term need for your inventory, consider lending materials or props to other organizations in your sector. Visit Barder.art to post materials to share, sell or give away.
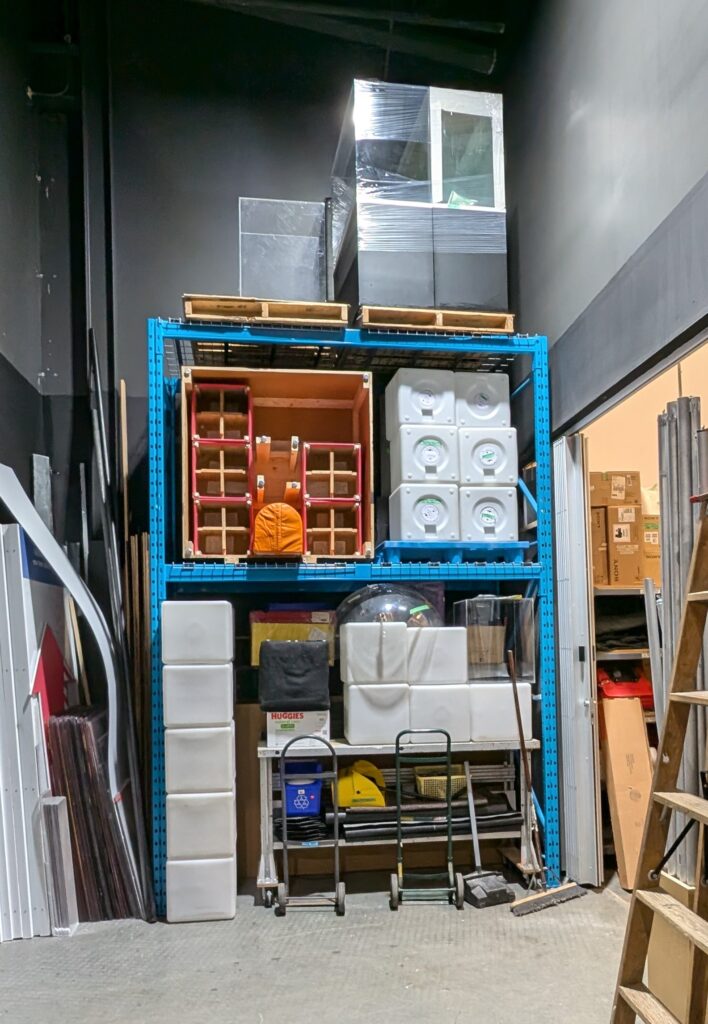
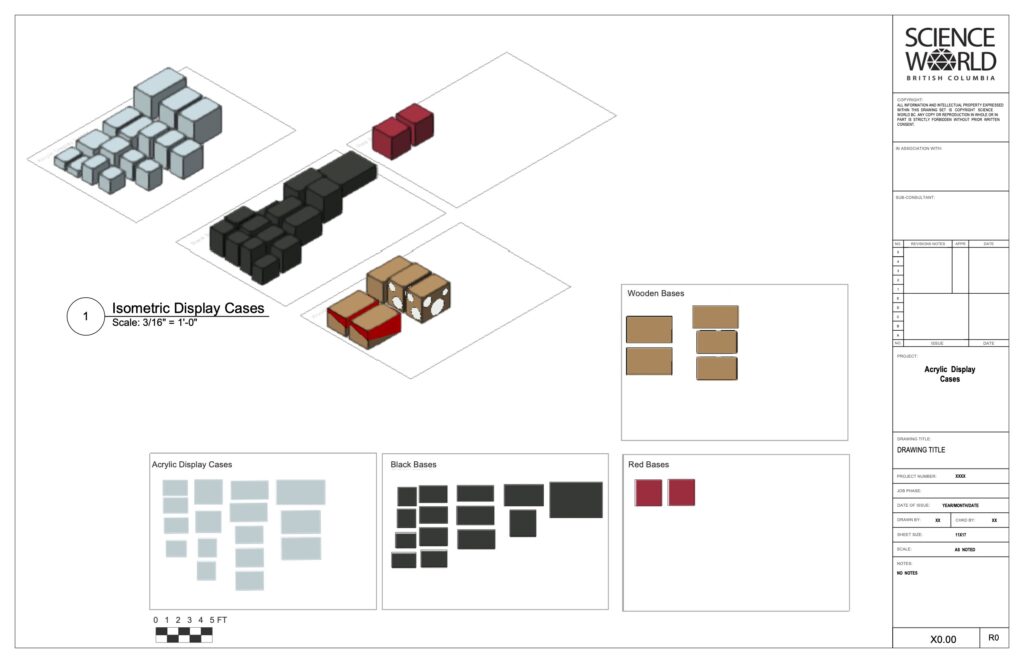
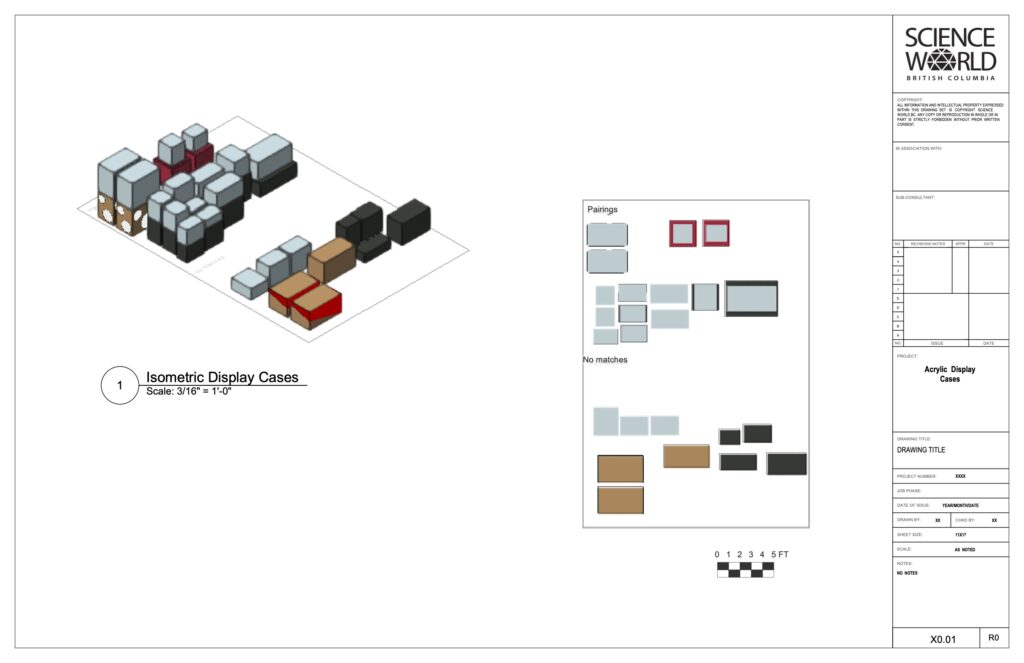
Before making new materials purchases, identify used materials or props and other elements that are appropriate to your production. Source used goods and materials available from other arts organizations (and beyond), and prioritize use of them over new goods and materials whenever possible for the exhibition or theatre set. In museums, using reclaimed materials or props may require decontamination, so project planning should allow time for that.
SAGE Exchange Hub
For galleries, museums and theatres in British Columbia, check out the Exchange Hub for options for sourcing, selling, sharing or giving away materials and props.
Barder.art
For those outside of BC, visit Barder.art to check if people in your region are sharing materials on the platform. If not, consider rallying a critical mass of organizations in your area to take advantage of this fantastic free online resource.
For external service providers, include specifications for circular requirements in requests for proposals (RFPs), contracts for designers, and in bid construction documents. If you’ve taken the Project Pledge, you may refer to your commitments there.
Be as specific as possible in your specification about which of 5Rs commitments you want to achieve – and how you want to achieve them. For example, instructions for the designer could be: “All exhibit units must be design-for-disassembly to enable reuse later.” Avoid vague language, such as: “We encourage you to consider materials reuse in your design.” Include this language in documents for the management of the design and construction and deconstruction (unbuilding) stages with your team and with any contractors.
Provide guidance, to ensure contractors comply with your circular goals, and review the list of materials and assembly documentation as requested in bid or contract documents. Continuously look for ways to reduce waste and apply the 5Rs of circularity.
Adding Circular Commitments to Your RFPs and Contracts
Here is sample language to include in RFPs, bid documents and contracts for external service providers. You may choose to use all or some of this language. You may also find this content helpful when evaluating bids, or for use in applying for grants or awards.
Staged environments aim to enhance the visitor’s experience through a carefully crafted blend of function and design. While unleashing creativity for the next production, can planners, designers and fabricators also find ways to extend the life of materials and props for this project and projects that follow?
Toby Barratt, a partner and designer with Propeller Studios in Vancouver, British Columbia, comments: “Designers can view circularity as a challenge or guide to creativity, not to constrain it.”
Kick off and upfront engagement of the team may add to costs, but reducing waste, extending the life of materials and avoiding purchase of new materials may also save costs in this exhibition or the next one. This may require leaders and planners to think beyond one production or exhibition at a time. Will you invest in modular wall systems that will reduce materials requirements in future exhibitions? If you choose to purchase more durable products or materials, or to buy upcycled or recycled materials and they come at a price premium – are you able to amortize that cost of the reuse of the material over multiple theatre sets or exhibitions
Definition Upcycled
A blend of reusing and recycling, involving the creation of a new product from an old or waste item, often resulting in a product of higher value than the original.
Also described as recycling (something) in such a way that the resulting product is of a higher value than the original item (a discarded object). The phrase is often used in the world of home improvement and crafting. The prefix ‘up’ indicates that a previously used, now useless item is changed into something with a different function.
Definition Recycled
Materials and products that have been used before and then put through a (manufacturing) process to create new products with all or partial recycled content.
One challenge is the perception that it takes too much time to design, build or unbuild to avoid waste and ensure optimal reuse of materials. Disassembly vs. demolition in particular may take more time, especially until the team gets comfortable with new practices. We’ve also heard from builders that multiple (and last minute) changes to design specs leads to construction time constraints that hinder best practices in building or unbuilding to optimize materials reuse later.
Allow sufficient time for designers to source used materials and to design for circularity, and recognize that fabricators need time and knowledge of how to build or assemble and disassemble in ways that avoid waste and preserve materials for reuse.
Similar to good green building practices, whole systems thinking in the planning stage should lead to better outcomes and avoid bottlenecks later. The planning team needs to think about the 5Rs – and specific ways to deploy them at every stage in the development of exhibitions and other staged environments.
By establishing your organization’s commitment to circularity and engaging your team in the integrating of circular solutions, you will transform the culture of your organization. The aim is for zero waste and circular production to become a challenge and opportunity for sustainability leadership, not a constraint to creativity.
For inspiration, share examples of circularity from other theatres, galleries and museums, and use both the Organizational Pledge and the Project Pledge to put your commitments in writing – and share with your team and with your audience.
What if you’re a contractor and the client does not indicate waste reduction or circularity is part of the project goals? Can you propose zero waste solutions anyhow and differentiate your company or contract services with your knowledge and ability to integrate circularity into your services? Share this toolkit with other organizations for a start.
Definition Zero Waste
Designing and managing products and processes to avoid and eliminate waste, and conserve and recover resources. Zero waste is an outcome of circular practices. See also: Zero Waste Hierarchy under “When You Must, Recycle”.
While the theme and focus of your theatre production, gallery or museum exhibition may not focus on climate, the environment or circular economy, can you find ways to share your circular achievements and outcomes through signage, digital messaging or other means? This sector has the opportunity to influence cultural transformation towards environmental sustainability and showing how you achieve it in your exhibitions and theatre events may inspire action beyond your doors.
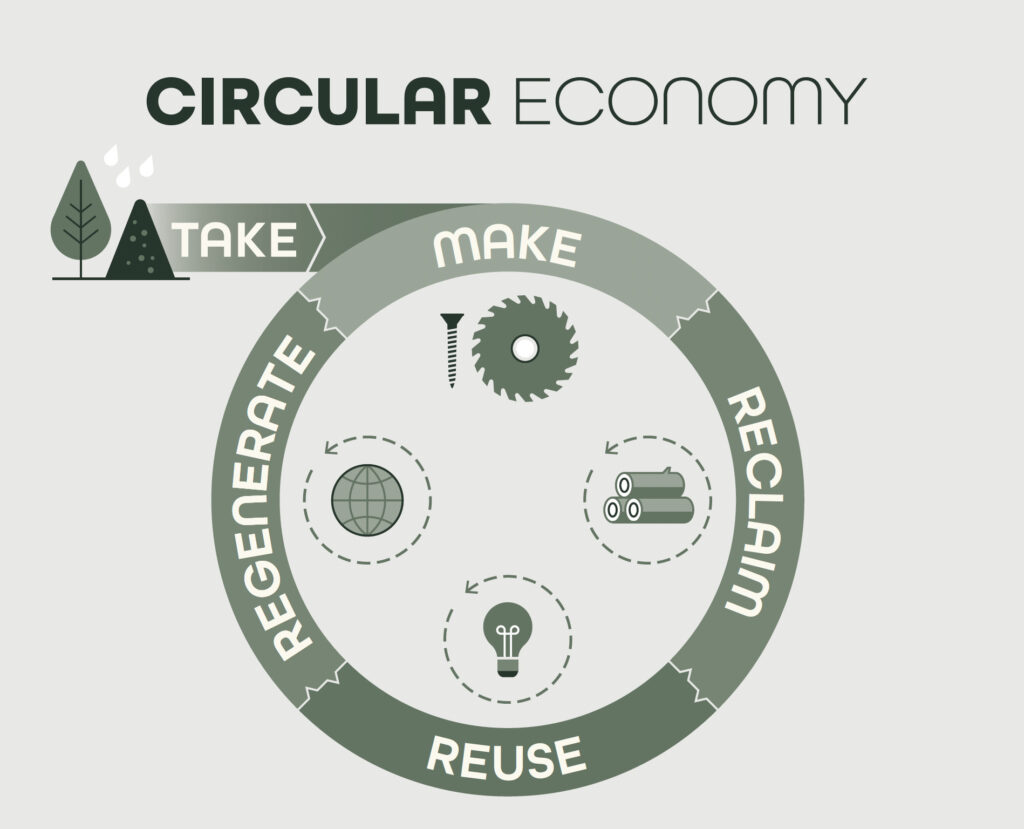
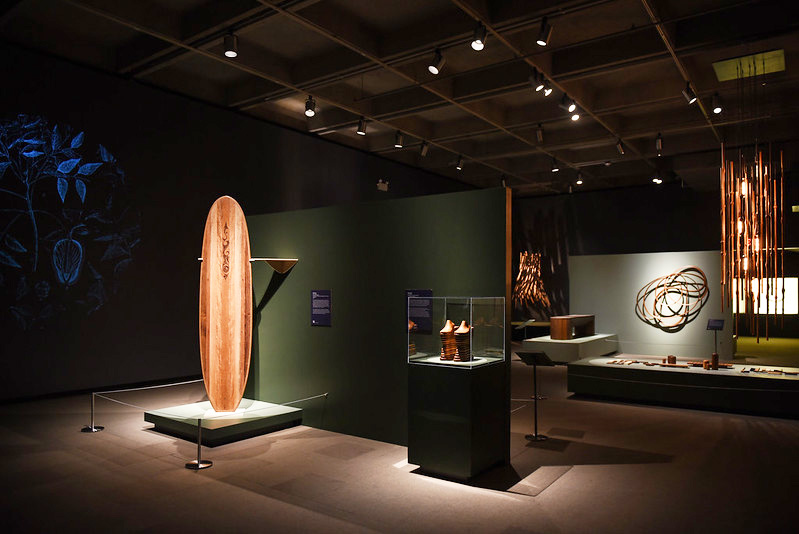
Case Example: Rethinking the Planning Process to Maximise Materials Reuse
The Museum of Communication in Bern, Switzerland, set a goal to reuse 95% of the materials and equipment in their Planetopia exhibition. This led to rethinking how to plan and develop exhibitions to avoid waste and extend the life of materials and equipment.
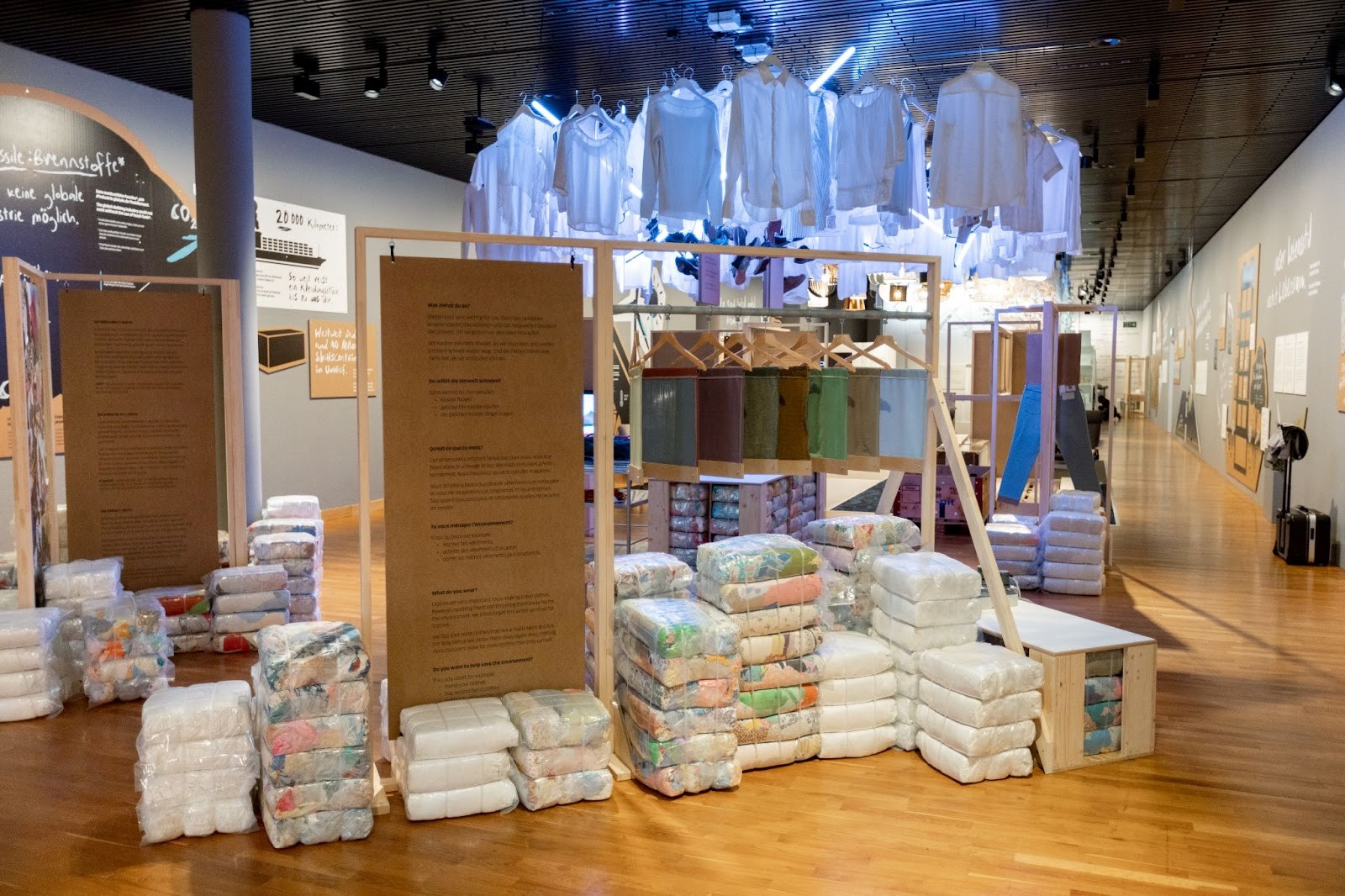
Case Example: From Sustainability Themed Exhibition to Planning for Circularity
When planning documenta fifteen exhibition, the Museum Fridericianum in Kassel, Germany began exploring the environmental impacts of their exhibitions. This led to lasting change, with circularity now integrated into planning and development of all their exhibitions.
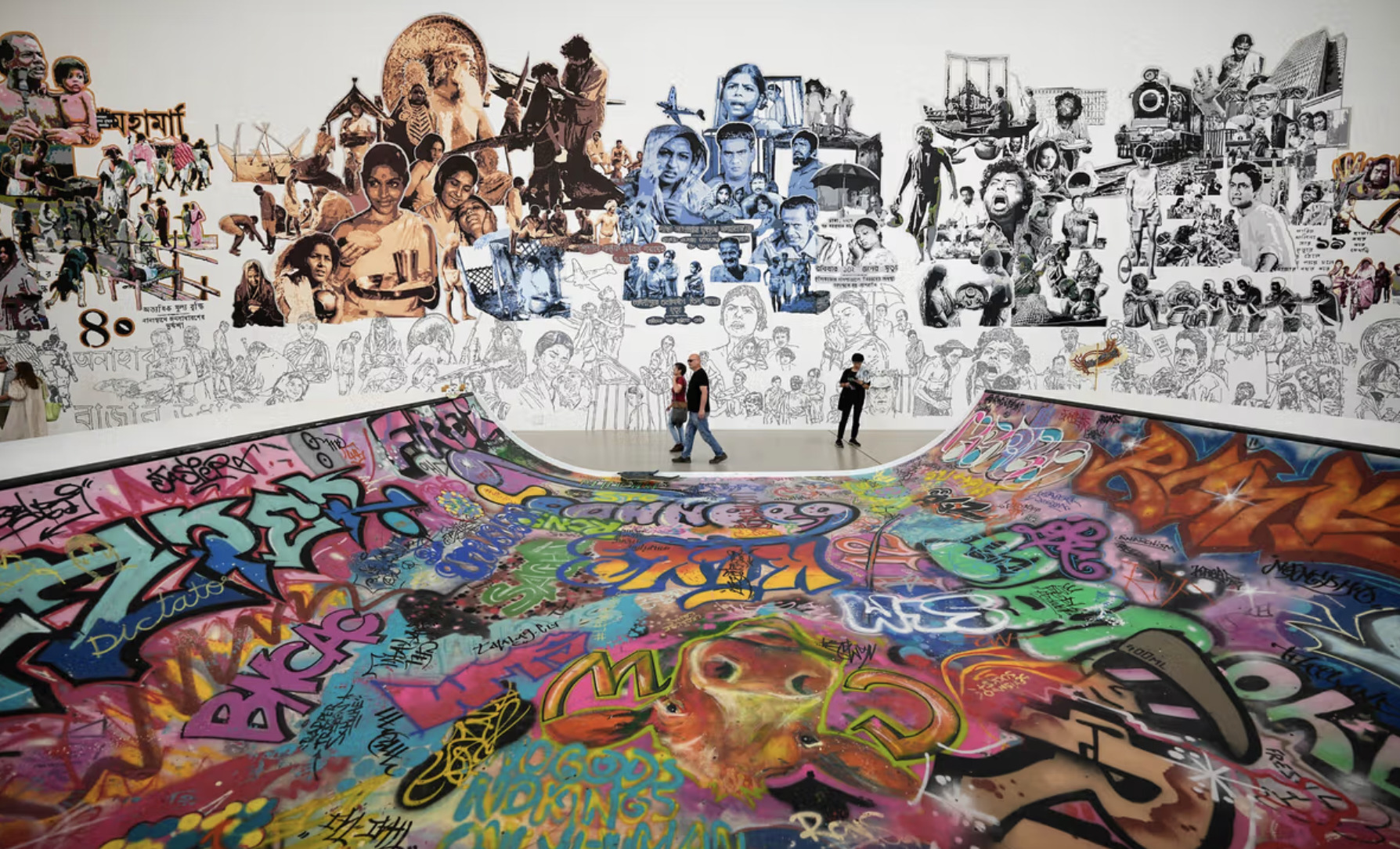
Designers conceptualize, create and help execute museum and gallery exhibitions and displays and other types of staged environments. The design stage is a critical time to embed circularity goals and sustainable practices directly into each project, ensuring environmental commitments are integral from the outset. Which of the 5Rs circularity principles are relevant to the particular project? How can they complement or coexist with other design elements in order to design out waste?
Definition Principles of Circularity (the 5Rs)
The principles of circularity are based on the idea of creating a regenerative economy that eliminates waste and pollution, keeps materials in use, and replenishes natural systems. The 5Rs circularity principles are: Re-think, Refuse, Reduce, Reuse, and Re-circulate. See Circularity.
For exhibitions and other staged environments, the SAGE toolkit focuses on the above five (5) key principles of circularity. The 5Rs guide planning, design, materials selection, building and disassembly of staged environments. There are additional “Rs” among circular principles, some more relevant to manufacturers or government waste management practices. See the 5 Elements: Planning for more detail.
Quick Tips
Here are quick tips summarizing how to plan circular exhibitions and other staged environments. Visit How To Design Circular Exhibitions for more details.
Rethink and Refuse
- Challenge designers to rethink design to design-out waste.
- Design with what you have – check your inventory.
- Borrow and share to extend the life of other materials.
- Maximize materials use and minimize offcuts.
- Refuse high carbon and toxic materials; choose durable and regenerative materials.
Design for Today and the Future
- Design for adaptability and design for disassembly to extend the life beyond one exhibition.
- Standardize pieces and elements for reuse across galleries or for future exhibitions and theatre sets.
- Invest in modular walls and modular design.
- Design and budget for this project and future staged environments to amortize design and materials investments.
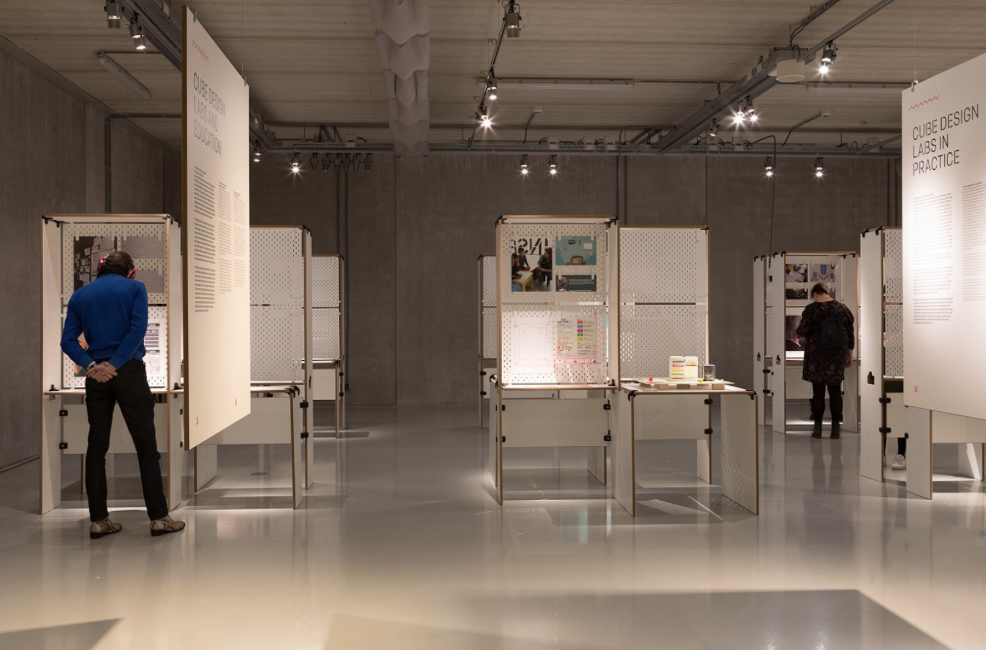
How to Design Exhibitions and Other Staged Environments
For many years, designers approached new exhibitions as blank canvas. Integrating circularity into design, does not detract from creating cohesive and visually engaging solutions that support the exhibition’s narrative. The aim is to achieve all that while incorporating the 5Rs of circularity, allowing us to create compelling, low-waste designs that minimize greenhouse gas emissions.
Definition Greenhouse Gas Emissions
Any time you purchase new materials and other goods for your exhibition, the manufacture and distribution (and sometimes the use) of those products generates greenhouse gas emissions (GhGs). Also, when building and unbuilding your exhibitions, any resulting waste-to-landfill is another way you generate greenhouse gas emissions.
Can we rethink the design process to integrate circular principles while maintaining creativity and then effectively communicating information, ideas, stories or emotions? How can we design for circular staged environments? Here are key areas to focus on:
As in the planning stage, designers should start by surveying existing materials inventories and survey exhibitions that will be disassembled, in order to identify materials reuse. How can the new exhibition repurpose walls, risers, and other materials, while creating something fresh and new?
Does every element need to be new and different? The Museum of Modern Art in New York (MoMA) is now challenging their designers to rethink creativity while standardizing their display cases to facilitate reuse (or recirculation) of the cases in all their exhibitions.
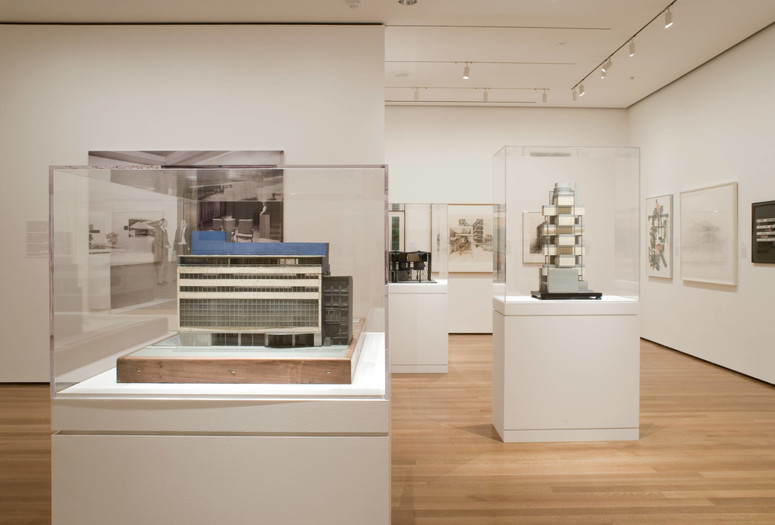
Use Barder.art and other exchange platforms or networks to source used materials and props beyond your own theatre or gallery that are available to borrow, buy or collect for free.
Can you rethink ways to be innovative and interesting without generating a lot of waste from offcuts in the fabrication process, or waste generated by materials that are not suitable for future reuse?
For the Museum of Vancouver’s (MOV) Reclaim + Repair: The Mahogany Project, the designers, Propeller Studio, opted to paint circular shapes on the plinths and risers rather than cutting them into the wood, effectively eliminating offcuts. For their Dressed for History exhibition, MOV borrowed heavy translucent draperies from the UBC Museum of Anthropology for two years. They used the curtains as wall dividers, avoiding the need to build walls, while using a durable, used and reusable material that complemented the theme of the exhibition.
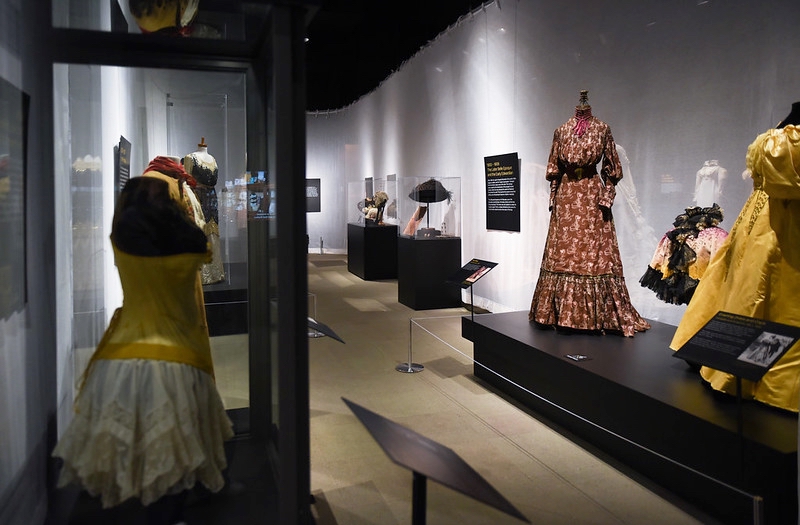
Designing out waste ideally includes extensive use of repurposed structures and materials and elements. When using new materials:
- Use durable materials that can be reused.
- Minimize cutting (to optimize re-use).
- Use standard and larger cuts to optimize potential for reuse.
- Design structures to be deconstructed (joinery considerations) and fully reused.
Case Example: Design Out Waste in Plywood
See how design consultant Goodweather maximizes use of a commonly used material in staged environments: plywood sheets.
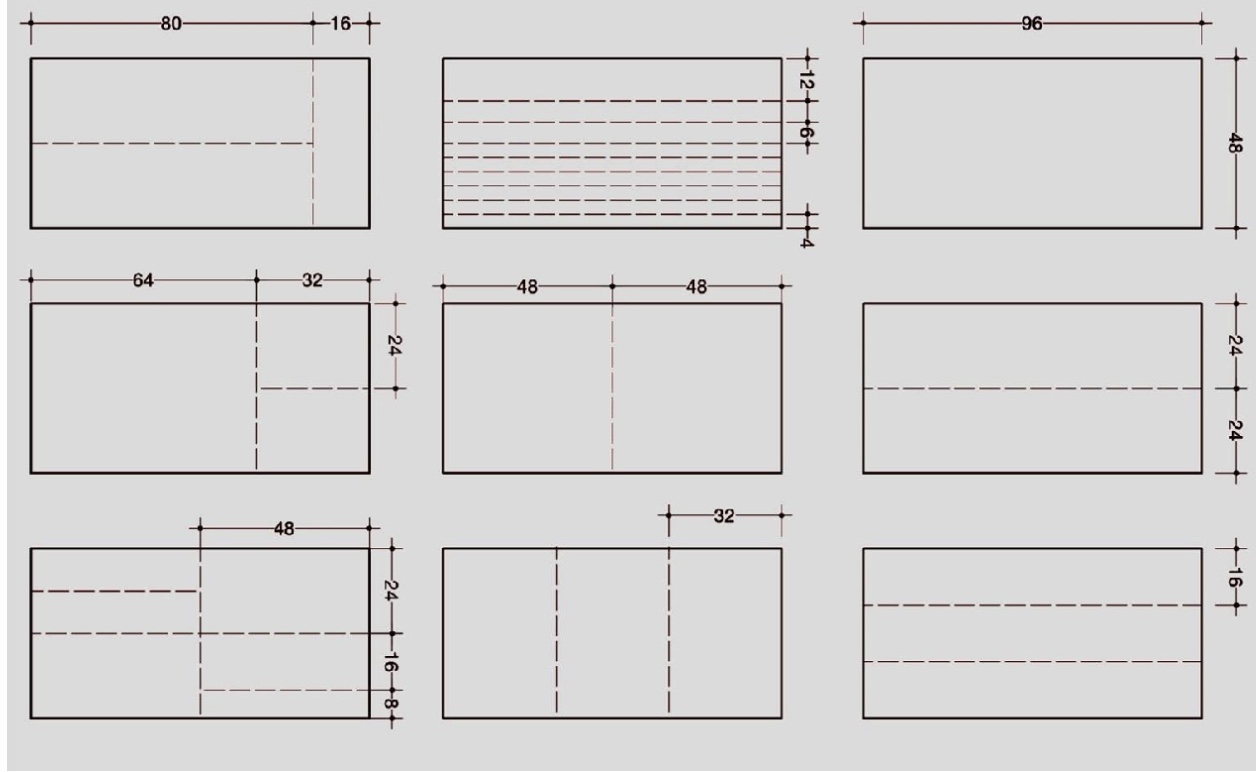
Another way to design out waste is Design-for-Disassembly. This is a concept that has been adopted for circular practices by leading companies in the computer and car manufacturing sectors. Recognizing there are valuable materials to reclaim for reuse, re-manufacture or reuse – and wanting to avoid disposal costs, manufacturers recognize that in order to be easily disassembled, the products must be designed and manufactured to enable it.
DfD is a set of principles that guide the design of products and buildings to make them easier to disassemble for reuse, repair, upgrade, or recycle. For staged environments –applying DfD principles requires designing walls, risers, tables and other objects – ideally so they can be disassembled and reassembled for reuse in later exhibitions or theatre sets. This requires considering the joinery as well as the assembly and disassembly techniques by the fabricating team. Use of glue will help expedite the building process, but it will prevent disassembly of staged environments and reclamation of materials for reuse. For more discussion visit Building and Unbuilding.
Design-for-disassembly is particularly useful if materials will be stored for reuse later or shipped for re-assembly at another location, because disassemble structures are more compact.
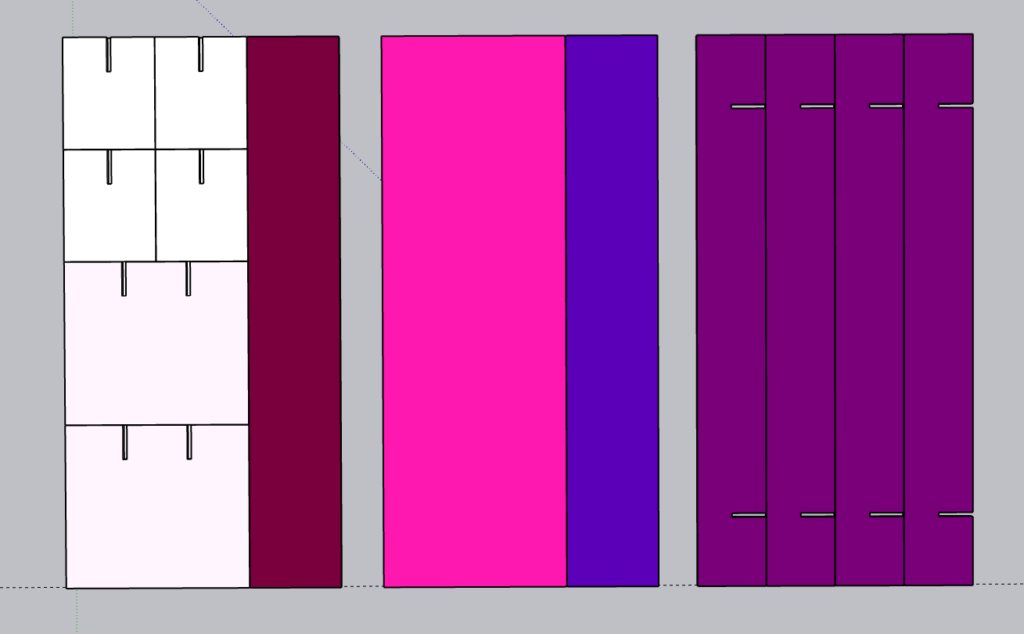
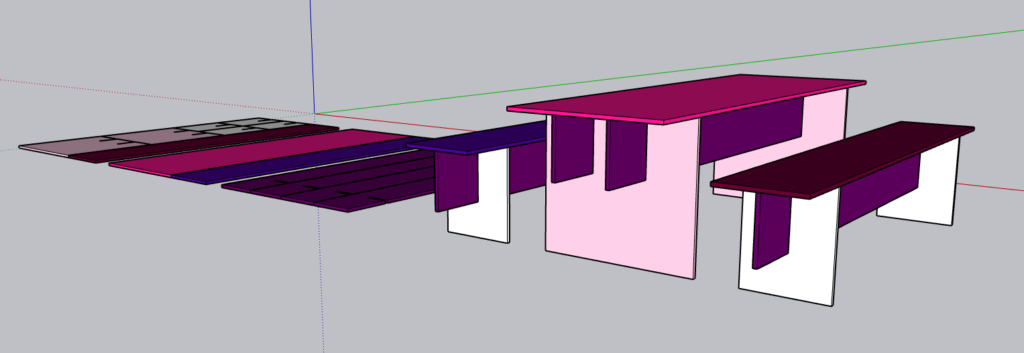
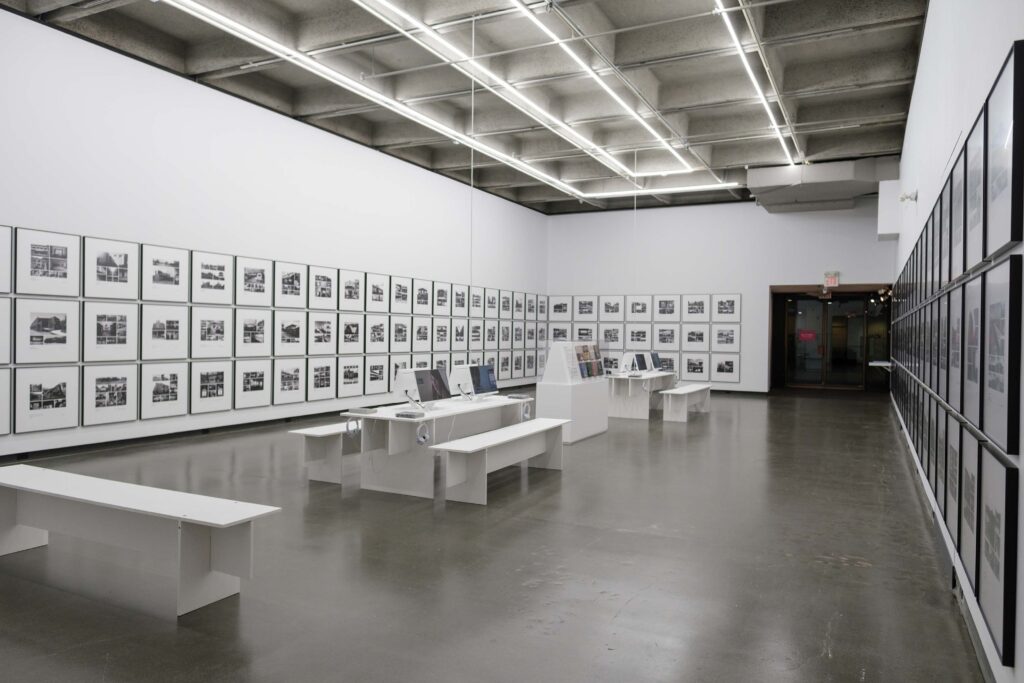
A close cousin to DfD is Modular Design or Design-for-Modularity. A wall system or riser may be reconfigured into a different wall system or a display case or seating for visitors. Modularity challenges the designer to not only think of the immediate design of the exhibition or theatre elements, but how to design to enable them to create new and different lay-outs or uses of the modular units.
Definition Design-for-Modularity
Modular design is a design approach that involves breaking down a system into smaller, independent parts called modules. These modules can then be used in different systems, or combined to create more complex systems.
Good modular design encourages flexibility and creativity, and supports circularity because pieces can be reconfigured for reuse repeatedly.
Extensive use of modular cubes or other other structures for walls, risers, benches, tables, seating and other features will dramatically reduce waste associated with staged events. One challenge of modular systems is that, if they are not in constant use, they may require significant storage space. Designing modular systems that may also be disassembled and reassembled would enable more compact storage.
In their permanent exhibition, Planetary Crisis – To Continue Living on This Earth, The National Museum of Emerging Science and Innovation in Japan designed-for-modularity to enable change of the layout depending on the flow of visitors and positioning of exhibits. Designing for modularity required rethinking how various elements of the exhibition can be reconfigured.
Also, as is a consideration for design-for-disassembly, joinery is a critical consideration for modular systems. For this exhibition, furniture is assembled with mortise and tenon joinery, and the all-wood exhibition was constructed using screws and bolts and almost no glues.
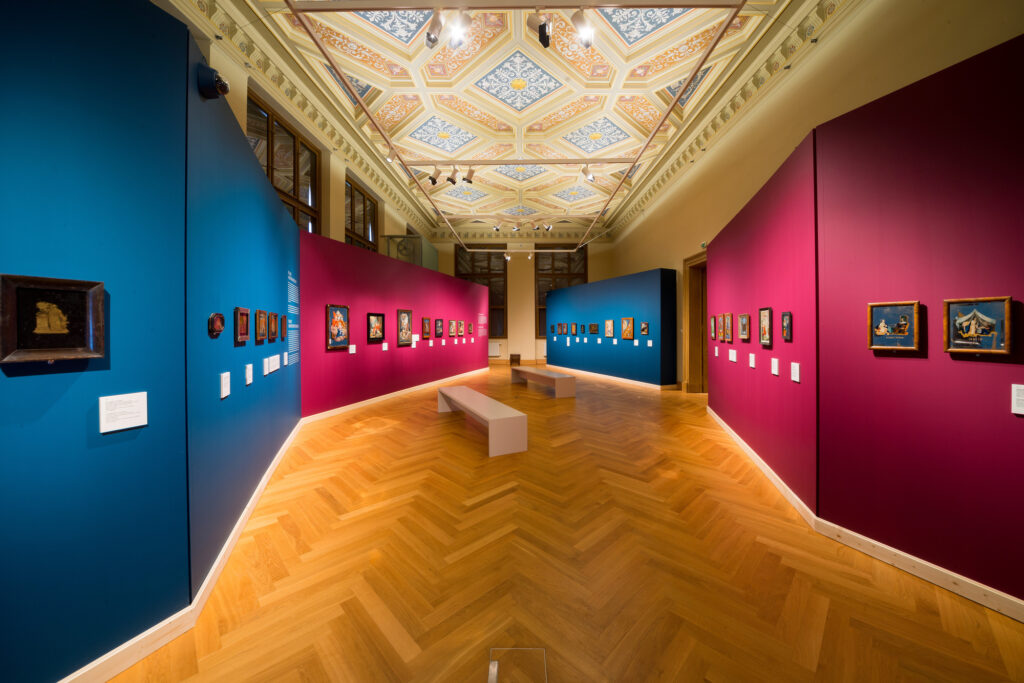
Rethink the design process to allow flexibility to adapt designs to better achieve the 5Rs. If reducing and avoiding waste is important – can you choose or adjust designs to avoid or minimize offcuts?
Focusing on use of wood in one of their permanent exhibitions, the National Museum of Emerging Science and Innovation in Japan cut their didactics from wood offcuts from the structures, and even stacked small wood offcut pieces to make legs for tables. These design solutions came as they identified waste wood that would be generated in cutting the larger structural pieces.
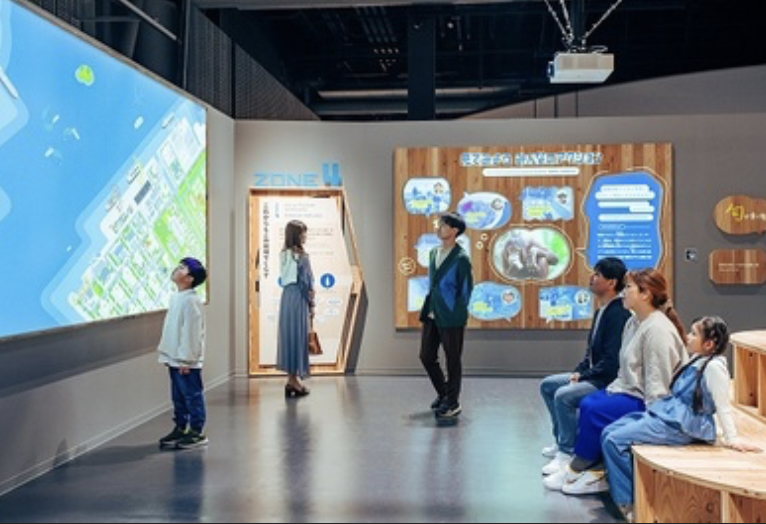
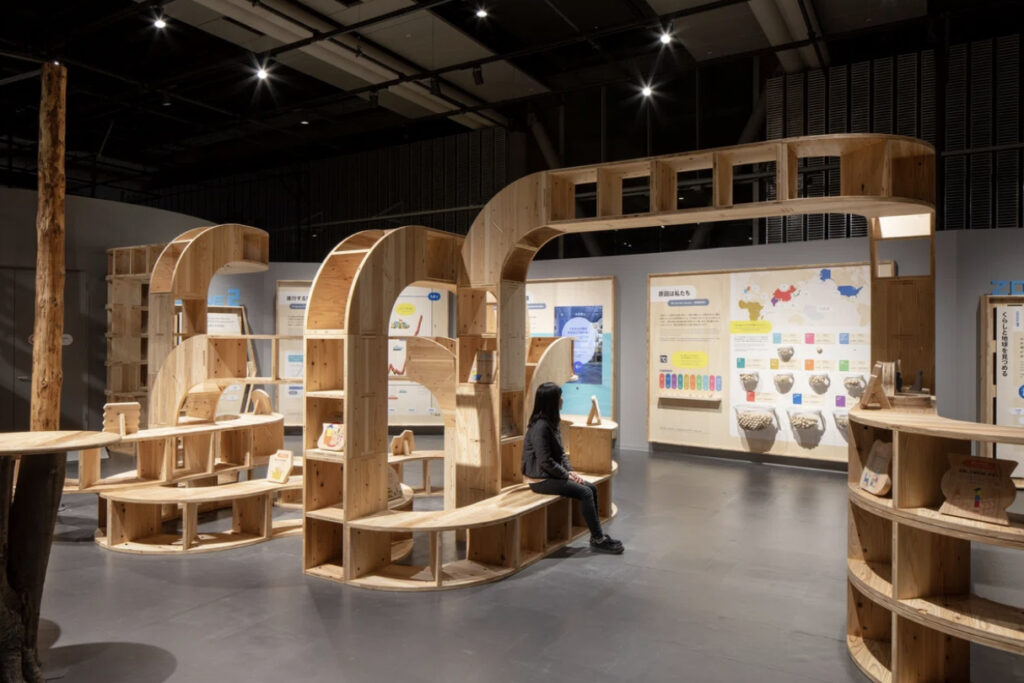
In circular economy thinking, designers ideally aim for use of existing assets to reduce waste and to refuse purchase of new material. They also consider how to extend the life of exhibition elements such as walls, pedestals, risers or display cases. Consider durability and flexibility over the longer term of the materials you choose and the objects you design.
The designs should be flexible and adaptable to address current needs while designing to enable reuse or reconfiguration in future staged environments. You may need to rethink your budget and plans beyond the immediate next theatre set or exhibition. Consider commonly used items and objects – can you amortize the cost to design and build or purchase items, such as modular walls, over a longer term?
Circularity is one of the principles of regenerative design. Design of exhibitions and theatre productions with an environmental theme, will likely include natural materials. However, circular designs may also integrate use of regenerative materials.
Regenerative materials not only reduce environmental harm but also have properties that promote ecological balance, support sustainable resource management, and foster environmental restoration. Bio-based materials, such as bamboo, straw and hemp-based and other natural fibre, and sustainably-sourced nature wood and timber are some types of regenerative materials.
Definition Regenerative Design
A process that aims to create a positive impact on the environment by mimicking the restorative aspects of nature.
Some principles of regenerative design include:
- Holistic thinking, i.e., a design approach based on the idea that all things in nature are interconnected, and that what benefits one thing likely benefits another.
- Focus on potential, i.e., a focus on the intended effect and outcome of the design such as avoiding waste and creating opportunities for reuse.
- Analysis of place, i.e., analysis of space that evaluates how a space functions and interacts with its environment, considering its physical layout and broader ecological, social, and cultural impacts. Examines how the space is used, its effect on the environment, and its potential to regenerate rather than deplete resources.
- Biodiversity, i.e., design that promotes environmental sustainability, the health of ecosystems, life and dynamism.
- Circular economy, i.e., a system where materials never become waste and nature is regenerated. Circular design aims to reduce and eliminate waste, recirculating products and materials for reuse, and refusing to use materials that are high carbon or environmentally damaging.
Case Example: Design Reset for Circularity at MoMA
New York’s Museum of Modern Art (MoMA) committed to advancing sustainability in how they operate the museum. The museum’s director challenged the museum and its staff to reduce the amount of waste it produces by 50% by 2025.
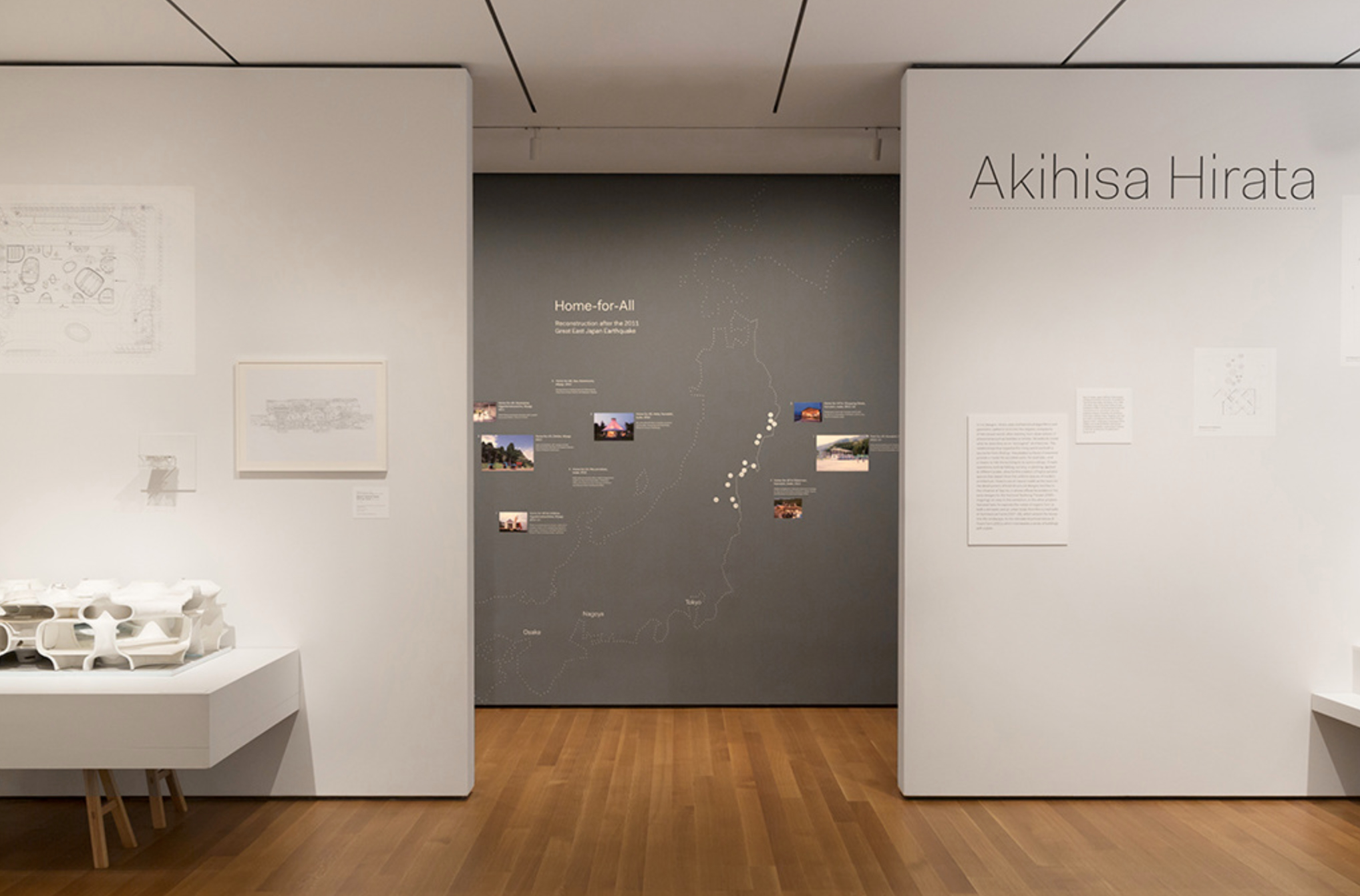
Case Example: Reclaiming Circular design at MOV
The Museum of Vancouver’s Reclaim + Repair: The Mahogany Project challenged the design team to apply the 5Rs. It was a fitting complement to the exhibition which features pieces created from vintage mahogany.
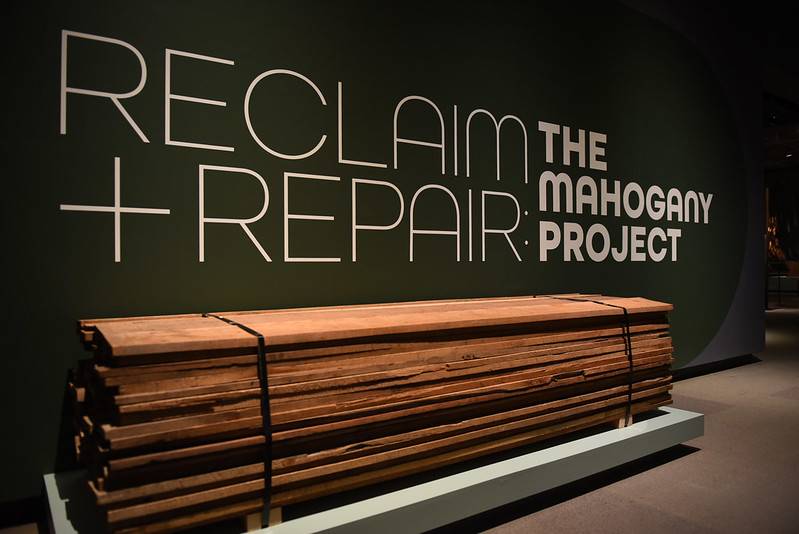
Circular practices have much to do with materials. Can we minimize waste of materials? Can we reuse or repurpose materials? Can we recirculate them to extend their life? But what about the choice of materials? What are key considerations for materials selection in planning and designing theatre sets and exhibitions?
Quick Tips
- Prioritize reusing and repurposing materials over buying new ones. Collaborate with a conservator to ensure reused materials are treated to stay pest-free and avoid contaminating artifacts in galleries.
- Select upcycled and recycled materials when purchasing new goods and materials.
- Choose durable and adaptable materials that can withstand repeated disassembly, while also considering embodied energy.
- Refuse materials with high embodied energy and other negative environmental impacts.
- Learn about regenerative materials and explore opportunities for their use.
- Explore alternatives to disposable and plastic-based interpretive panels.
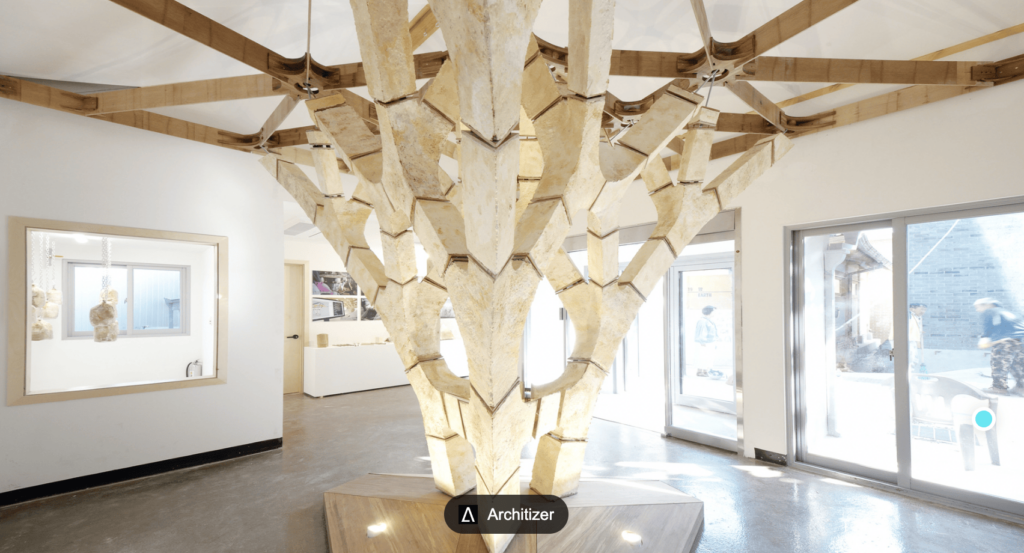
How to Integrate Circularity into Materials Used in Staged Environments
The choice of materials for exhibitions and staged events has traditionally been driven by the theme and design. What if you established guidelines about selecting materials that support circularity and help your stage events to avoid greenhouse gas emissions (GhGs)?
Here are a variety of considerations for your materials choices:
Whenever possible and appropriate for your project, the best choice is to reuse materials or structures you have already used. If you can source used materials from your local arts community and other local sources is also high up on the zero waste hierarchy. Fundamental to circularity is extending the life of materials for as long as possible.
The opportunity to extend the life of materials is influenced by its prior uses. Did the designers and fabricators use the materials to enable reuse and adaptability later? Highly customized shapes, for example, will limit the versatility for future reuse of a piece of plywood or other panelling. Were the materials assembled and disassembled with attention to minimizing damage in order to preserve the materials for reuse?
For example, for the exhibition Wild Things: The Power of Nature in our Lives, the Museum of Vancouver (MOV) met their target of target of 70% reclaimed material. MOV’s Director of Collections and Exhibitions, Viviane Gosselin, said “we struck gold” sourcing more than 60 sheets of used plywood and conglomerate that had been used on a film set. The materials were free, the only cost was for MOV to transport them locally. Displays in the first 2000 sq. foot gallery were a mix of reuse and recyclable materials and 30% of the displays in the second gallery used salvaged materials, and planning of the project included a deconstruction plan in place for all the materials used in the exhibition. Importantly, the curator collaborated closely with the conservator on staff to ensure that the plywood was pest-free before being used as construction material in direct contact with museum artifacts. Upon arrival, the material was cleaned, isolated, and wrapped in plastic sheets for several days prior to fabrication.
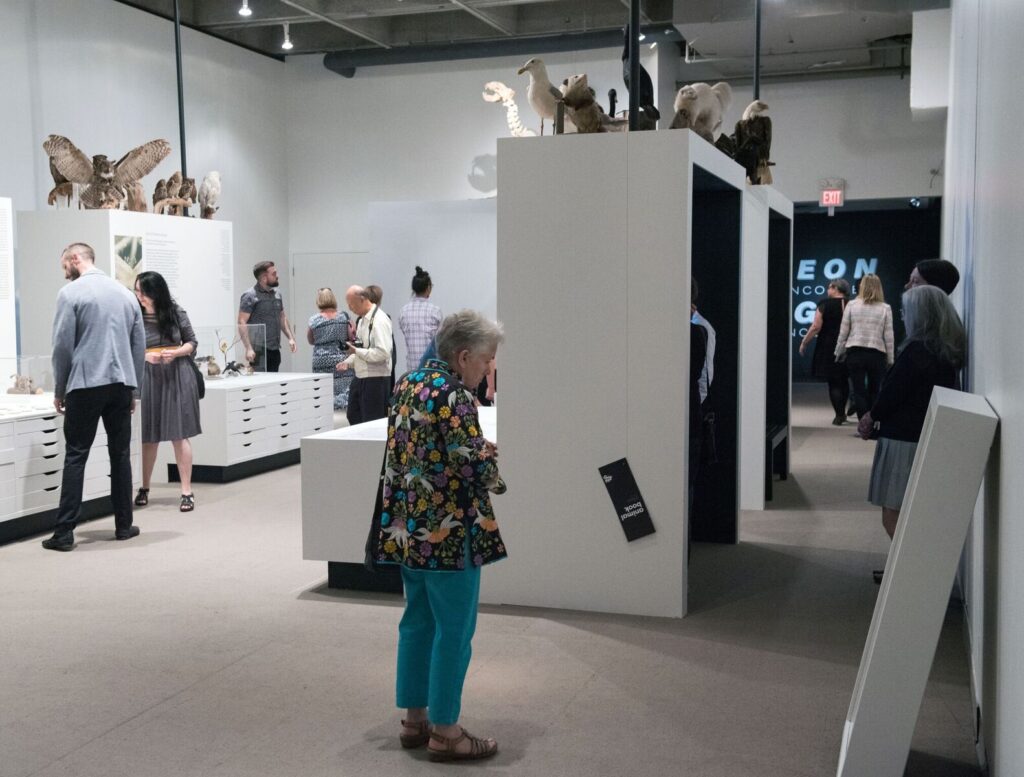
The UK-based design studio and production company 59 Productions recognized that the materials used in their designs were a significant source of greenhouse gas emissions. They sought to identify lower-carbon alternatives and empower their staff to make environmentally sustainable choices.
The studio worked with not-for-profit environmental organization, ReLondon, to develop circularity practices and lower carbon materials options for the theatre sector. ReLondon helped them understand that materials reuse should be a priority, so they explored the challenges of design-for-disassembly and deconstruction practices.
They also set up a digital catalogue and a physical material archive to display samples and products of preferable alternatives to their standard materials. ReLondon assisted the team in defining a hierarchy of preferred materials and products, and developing an easy to use ‘traffic light’ rating system to highlight preferred materials based on environmental criteria.
Check out the SAGE Common New Materials Environmental Evaluation in Resources & Inspiration. SAGE makes use of a similar ‘traffic light’ rating system for three categories of commonly used materials in staged environments: framing materials, panelling and paints.
Recognizing that you may not fill all your materials requirements by saving, salvaging and sourcing used materials, another option is to source materials that are made from used materials. This includes upcycled and recycled materials.
Definition Upcycled
A blend of reusing and recycling, involving the creation of a new product from an old or waste item, often resulting in a product of higher value than the original.
Also described as recycling (something) in such a way that the resulting product is of a higher value than the original item (a discarded object). The phrase is often used in the world of home improvement and crafting. The prefix ‘up’ indicates that a previously used, now useless item is changed into something with a different function.
Definition Recycled
Materials and products that have been used before and then put through a (manufacturing) process to create new products with all or partial recycled content.
There is an increasing number and type of products and materials in the market that are 100% recycled content, or partially recycled content. This may be textiles, drywall, furnishings, lumber and computers and other equipment. Establish a purchasing policy for your goods and materials for each exhibition (take the Project Pledge) and even across your entire organization. This may also include a policy for purchasing your digital equipment, though opportunities for purchasing recycled electronics remain limited. Consider Energy Star certification for energy efficient equipment and refurbished equipment.
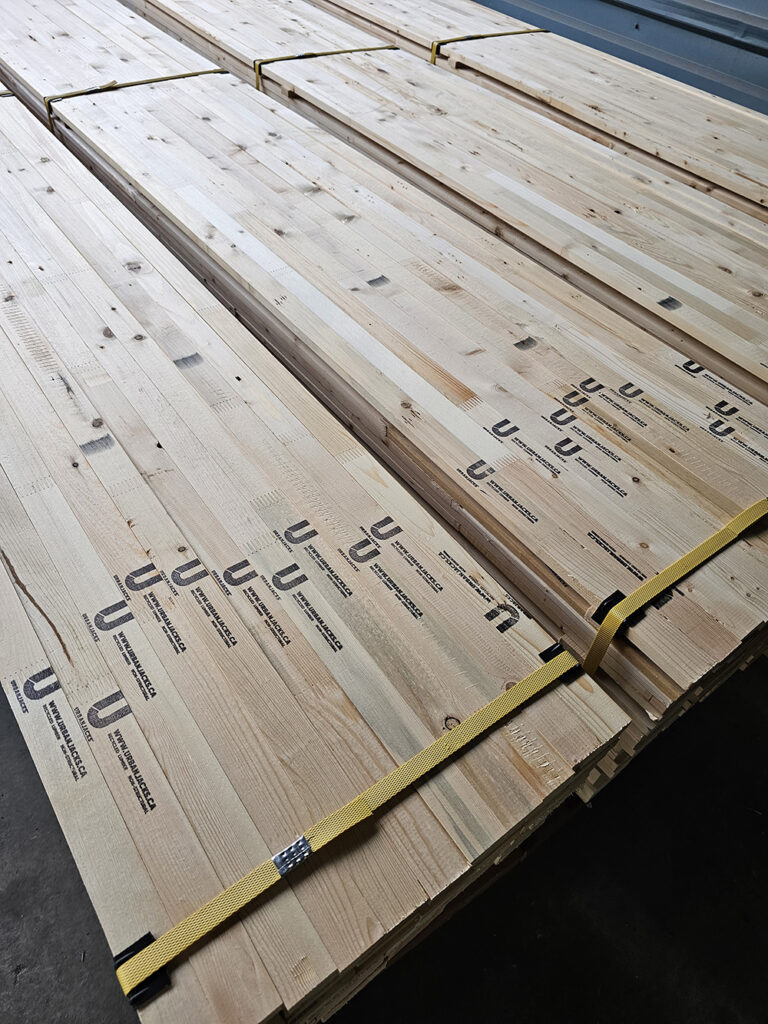
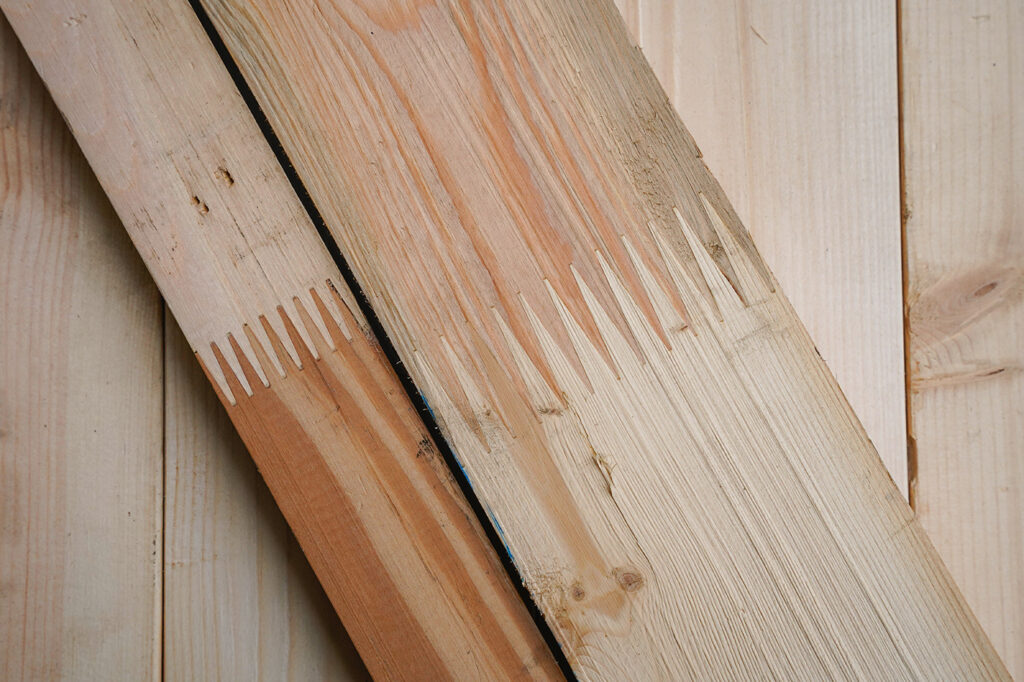
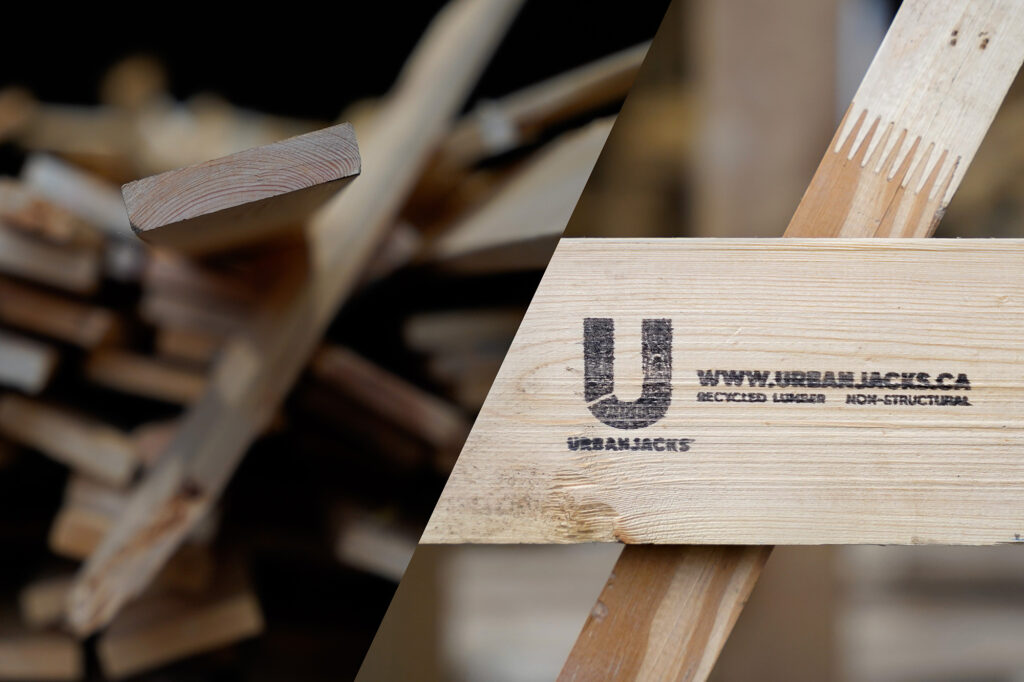
When sourcing new materials, consider their life beyond the immediate next exhibition or theatre set. Is the material durable and can survive repeated assembly, disassembly and (perhaps) reconfiguration. This is an important consideration for modular systems as well as any materials if you aim to extend their life.
While durability is important to the lifecycle of materials, what is a reasonable expectation for the life of materials when they are repeatedly manipulated with the turn over of staged environments?
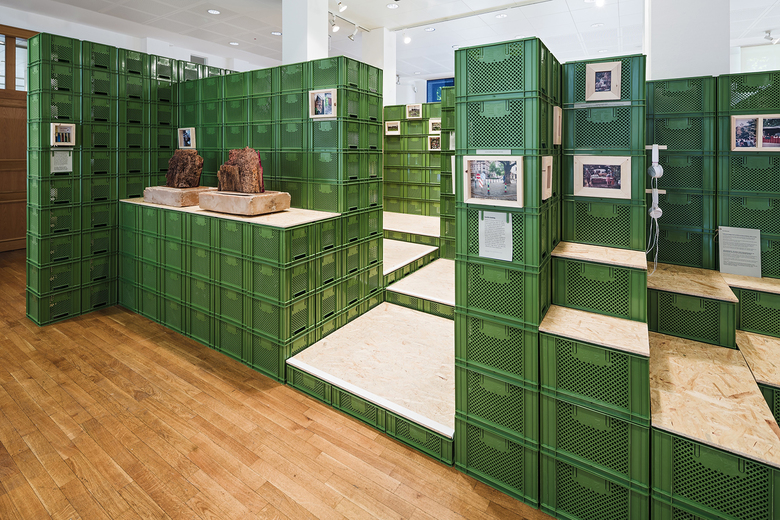
The Ernst-Bloch-Zemtrum museum in Ludwigshafen am Rhein in Germany, built the exhibition Heroes of the City entirely from plastic crates. These modular materials are very durable and can be constantly reconfigured and reused. However, the fixed colour and block shape limits variety and creativity from one exhibition to the next.
Another consideration is the embodied energy of plastic crates. Plastic is most commonly made from petro-chemical materials with high embodied carbon. For this reason, sourcing goods and materials made from recycled plastic instead of virgin plastics will significantly reduce greenhouse gas emissions associated with their lifecycle. When available, bio-based plastics materials are even better because they are made from renewable nature-based materials.
Definition Embodied Carbon
The total amount of greenhouse gas emissions released during the life of a building or product. It includes GhG emissions from the extraction, manufacturing, transportation, construction, maintenance, repair, refurbishment, demolition, and disposal of materials and products.
Embodied carbon is often measured and reported as Global Warming Potential (GWP) because some emissions calculations are for future emissions if the building or product is still in use.
Note: “Carbon” refers to carbon dioxide which is just one of the 7 main greenhouse gas emissions. Some projects distinguish measurement of carbon dioxide from measurement of all 7 GhG emissions.
There is growing attention to the greenhouse gas emissions associated with materials. This includes the full life cycle impact of the materials. Basic greenhouse gas assessment may only consider the impacts of shipping materials, or the impacts of products that consume energy (such as lighting, electronics and digital equipment). Yet there is much more embodied carbon associated with materials when you consider their life from ‘cradle to grave.’
There are a growing number of calculator tools for evaluating the full lifecycle impact of products and materials. Green building design in particular is incorporating materials assessments based on Life Cycle Assessment. Most of these are fairly sophisticated software products that trained professionals use during building design and materials planning.
Definition Life Cycle
Includes the extraction of raw materials, production, shipping, use, and post-use phases of a product, material or service (including end-of-life waste or materials processing). See also: Life Cycle Assessment.
Definition Life Cycle Assessment (LCA)
A systematic process that evaluates the environmental impact of a product or service over its entire life cycle. This includes the extraction of raw materials, production, shipping, use, and post-use phases (including end-of-life waste or materials processing).
See also embodied energy. LCA measurement of greenhouse gas emissions over the life of a product or service is measured in Global Warming Potential (GWP).
Most LCA tools are overly complex for assessing the greenhouse gas emissions associated with staged environments. With the emergence of GhG calculator tools for this sector we anticipate they will expand to include materials assessments. A Vancouver-based group has developed one called CarbonSimple.
CarbonSimple Project Estimator for Embodied Carbon of Materials
Created by the Arts Factory Society in collaboration with UBC Department of Forestry, CarbonSimple is a free online tool for project managers, designers, fabricators and producers to assess the greenhouse gas emissions (GhG) associated with staged environments.
CarbonSimple integrates seamlessly with cost estimation workflows, enabling calculation of the global warming potential (GWP) of material goods, labour, and transportation before making purchasing decisions or providing quotes to clients. GWP calculations include commonly used materials, reusable components and company-specific labour tracking.
You can also use CarbonSimple to assess annual budgets or review the GhG emissions of past projects or productions.
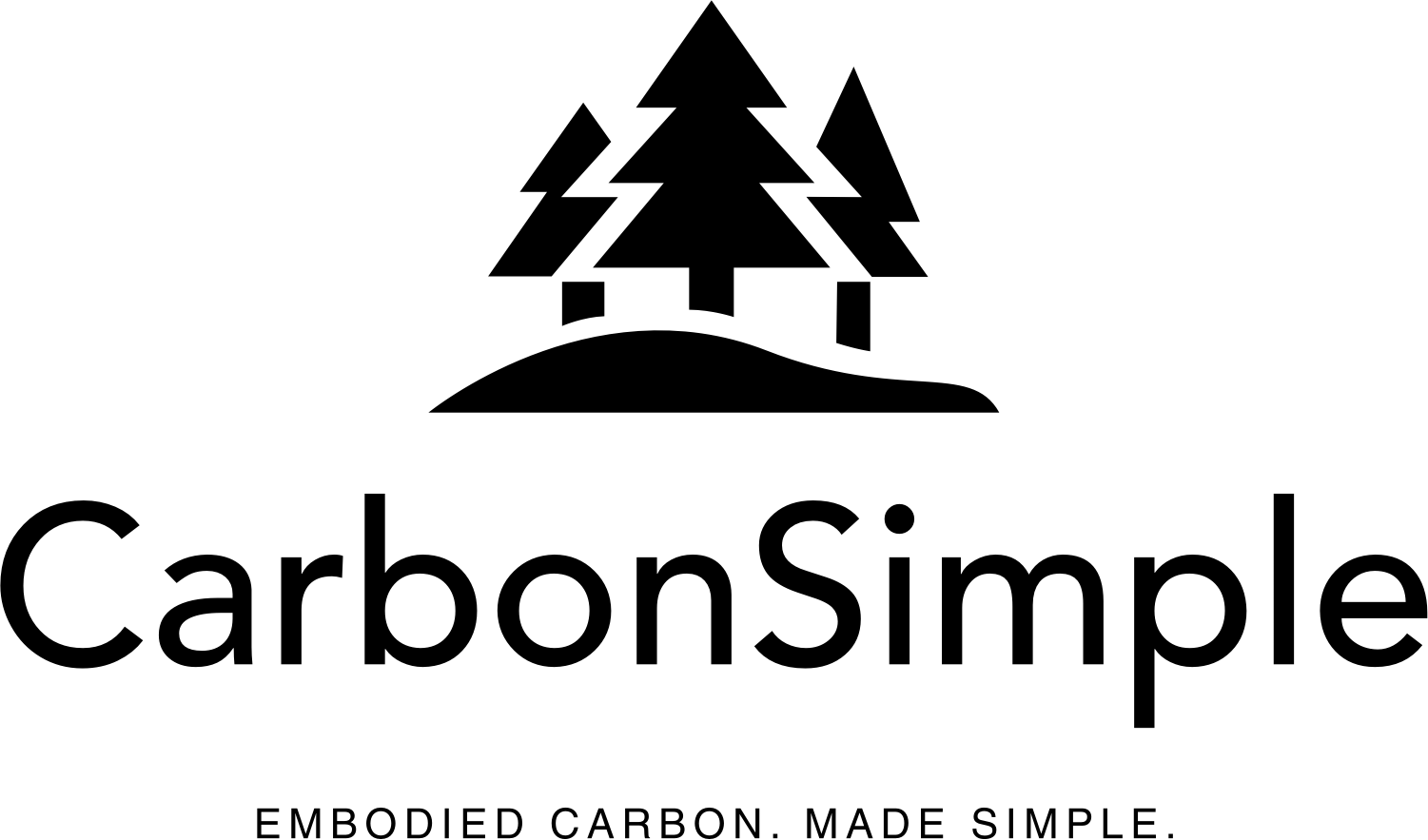
While there are a wide variety of materials and products used in staged environments, the SAGE Project identified and assessed materials that made up a significant portion of materials for most staged environments in Canada. These include lumber and other framing materials, plywood, MDF and paints.
SAGE worked with a Sustainability Scholar from the University of British Columbia to assess and rate the environmental impact of these materials categories. Reviewing a variety of framing materials, panelling and latex paints available in Canada, the team assessed their environmental impact based on a number of criteria including environment certifications, health and indoor air quality certifications and assessments, and Life Cycle Assessment. LCA assessment drew on environmental product declarations (EPDs) which quantify greenhouse gas emissions of products and materials over their Life Cycle.
Check out the SAGE Common New Materials Environmental Evaluation and New Materials Evaluation Summary for more.
SAGE developed a ‘traffic light’ rating system similar to the one developed by UK-based 59 Productions. SAGE rates materials giving them a ‘green light’ (or green colour) for materials and paints recommended for their lower LCA and other environmental impacts. Below that are ‘yellow light’ materials that have fewer positive environmental attributes, and third are items marked ‘red’ that we recommend avoiding. Here are a few highlights:
Framing Materials
Upcycled lumber scored the highest. Anytime you use an upcycled or recycled product you are dramatically reducing LCA because there is no impact of extraction and shipping of raw materials. UrbanJacks also scored highly because its use of a glue rated among the most environmentally friendly.
The SAGE evaluation assessed a number of specific brands of plywood sold in British Columbia. Visit to the Common New Materials Environmental Evaluation to see their scores and ranking.
The framing materials that ranked the lowest are metal and aluminum studs. While these materials may be advantageous for their durability and long life, the immense amount of greenhouse gas emissions associated with materials extraction and manufacturing would require you to reuse the materials for more than a hundred years to amortize the greenhouse gas emissions over time. Steel studs have 50 times more Global Warming Potential than lumber, and aluminum is even higher. if studs made from recycled metals become available, they may be a reasonable option.
Paneling
Plywood is a significantly better panelling option than MDF. Although you may prefer MDF for its smooth surface, this material has more than double the Global Warming Potential (GWP) of plywood. Plywood is also more durable for multiple uses, offering additional lifecycle advantages.
Definition Global warming potential (GWP)
When used in a Life Cycle Assessment (LCA), Global Warming Potential (GWP) is the metric used to measure the greenhouse gas emissions that will be emitted over the entire life cycle of a product, building, or process.
GWP is a measure of how much a greenhouse gas contributes to climate change and is quantified in kilograms of carbon dioxide equivalent (kg CO₂e). Specifically, GWP measures how much energy the emissions of 1 tonne of a gas will absorb over a given period of time, typically a 100-year time horizon, relative to the emissions of 1 ton of carbon dioxide (CO2).
Gases with a higher GWP absorb more energy, per ton emitted, than gases with a lower GWP, and thus contribute more to warming Earth. The most pervasive greenhouse gas, carbon dioxide (CO2), was assigned a GWP of 1. All other GhGs are multiples of this (e.g. Methane has a GWP of about 23 – or 23 times more potency for warming the planet than CO2).
Visit the glossary for a comparison of Building lifecycle vs. exhibition lifecycle.
Paints
There are a variety of bio-based paints, inks and coatings in the marketplace, with varying degrees of efficacy and appropriateness depending on their use in a staged environment. The SAGE research project focused on latex paints because they are so commonly used.
Not all paint brands publish their LCA, although some do. Our recommendation for paints is to choose those with credible third-party evaluation and certification, such as GreenGuard, Green Seal and Master Painter Institute’s (MPI) ‘extreme green performance’ evaluation. These consider both the environmental and health impacts of paints.
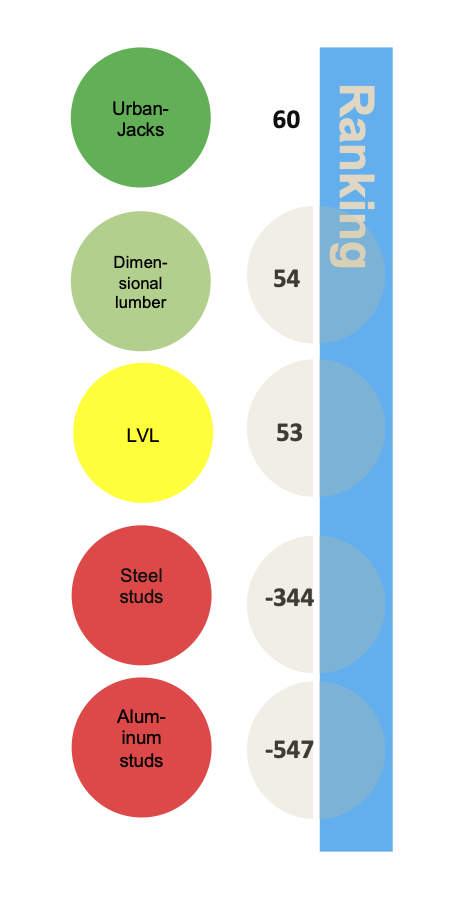
Cardboard has found its way into the design of exhibitions, theater sets, and other staged events. Since 2013, Opéra de Lyon has been using cardboard for the construction of its sets and accessories. This recyclable material was even used to construct a permanent base to which elements specific to each performance could be added. In Paris, the Théâtre du Châtelet is following the same practices.
This is unusual because most applications of cardboard are for short-term exhibitions and events. It lacks the durability required for some applications, but it has numerous environmental benefits, and it is lower embodied carbon than many other materials used for structures and didactics. It is also compostable and recyclable. Recycled cardboard, when available, is the ideal choice. Another advantage of cardboard is its lightweight and compact nature, which significantly reduces the energy use and greenhouse gas emissions associated with shipping compared to heavier materials transported by the same mode.
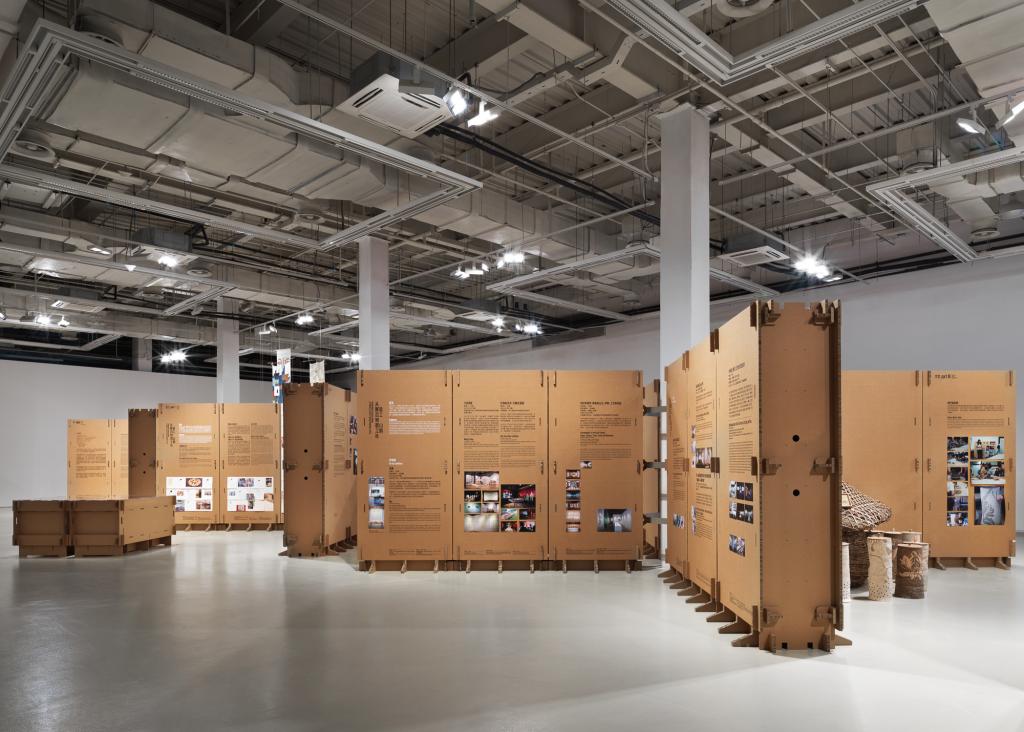
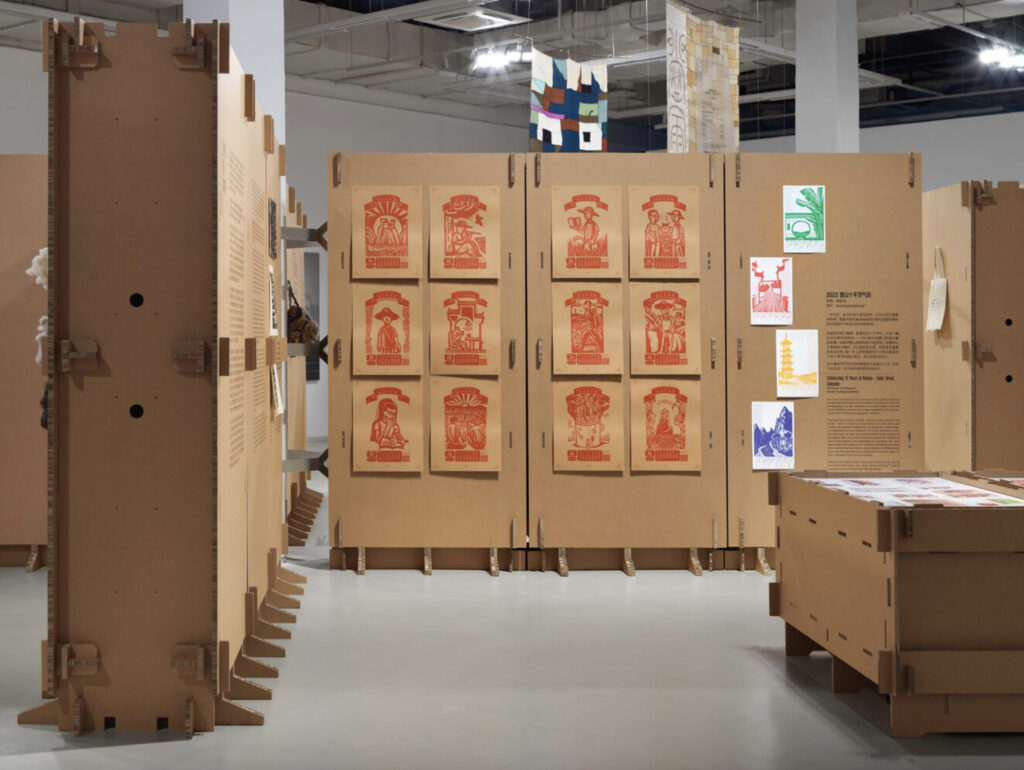
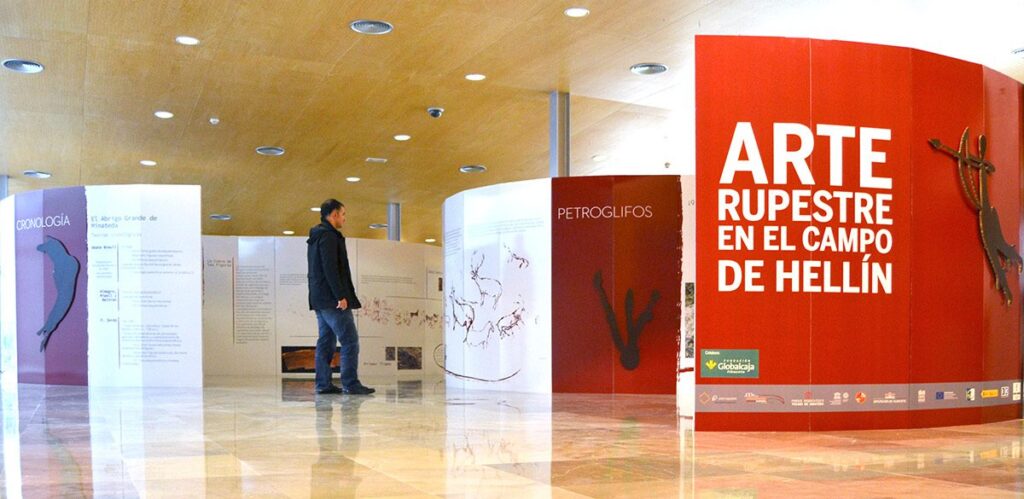
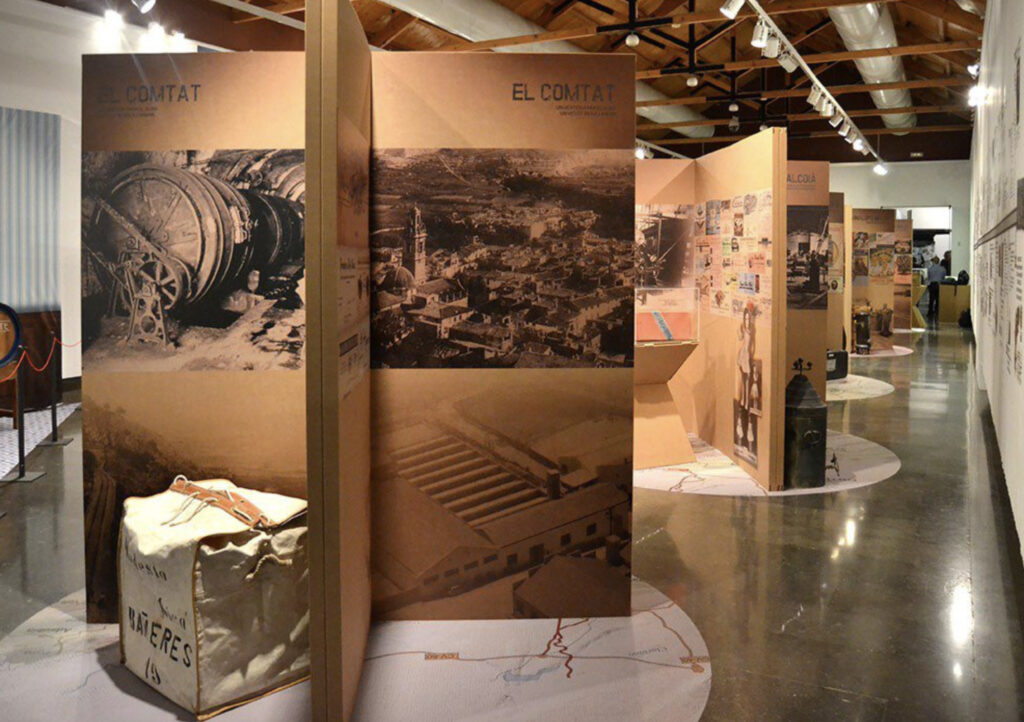
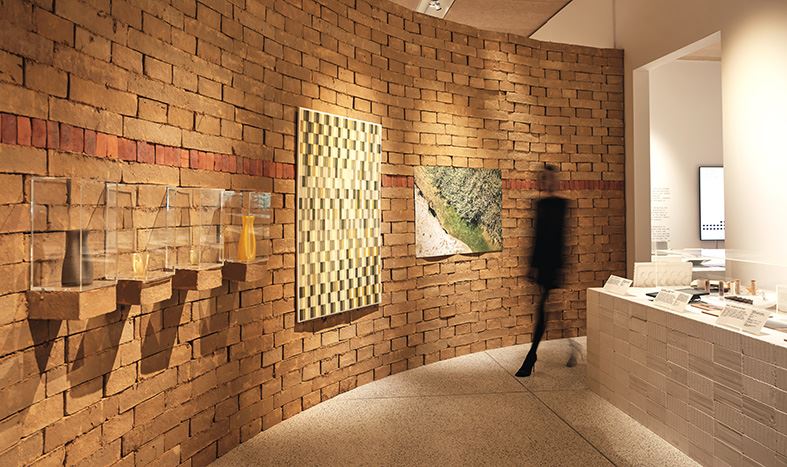
Circularity is one of the principles of regenerative design. Use of natural and bio-based materials does not need to be restricted to staged environments with an environmental theme. An increasing number of regenerative materials are available for producers of exhibitions and theatre sets. It may require stepping out of comfortable habits for materials choices, and it may take some experimentation to see how best to work with some materials.
Regenerative materials and products are made from materials that play an active role in restoring and regenerating natural resources, ecosystems, and biodiversity. They are defined as having properties that promote ecological balance, support sustainable resource management, and foster environmental restoration. From natural fibers to sustainable wood and timber, regenerative materials come in several forms.
Bio-based materials may not have such lofty goals, but they are made from biomass. Mycelium is a bio-based material that is gaining use in packaging, and has proven to have sound absorbing properties that may be beneficial in some applications.
Definition Regenerative Design
A process that aims to create a positive impact on the environment by mimicking the restorative aspects of nature.
Some principles of regenerative design include:
- Holistic thinking, i.e., a design approach based on the idea that all things in nature are interconnected, and that what benefits one thing likely benefits another.
- Focus on potential, i.e., a focus on the intended effect and outcome of the design such as avoiding waste and creating opportunities for reuse.
- Analysis of place, i.e., analysis of space that evaluates how a space functions and interacts with its environment, considering its physical layout and broader ecological, social, and cultural impacts. Examines how the space is used, its effect on the environment, and its potential to regenerate rather than deplete resources.
- Biodiversity, i.e., design that promotes environmental sustainability, the health of ecosystems, life and dynamism.
- Circular economy, i.e., a system where materials never become waste and nature is regenerated. Circular design aims to reduce and eliminate waste, recirculating products and materials for reuse, and refusing to use materials that are high carbon or environmentally damaging.
Definition Bio-Based Materials
Materials created using renewable biomass sources, such as plants, animals, marine, and forestry materials. Other possible sources include waste from sugar refineries and the production of biofuels, and algae. See also: Regenerative materials.
Definition Regenerative Materials
Materials that actively restore and regenerate natural resources, ecosystems, and biodiversity.
These materials not only reduce environmental harm, but also possess properties that promote ecological balance, support sustainable resource management, and foster environmental restoration. From natural fibers to sustainable wood and timber, regenerative materials come in several forms. Source: Tocco
Bio-based materials, such as bamboo, straw and hemp-based wallboard or building blocks, as well as natural wood or earth-based solutions are regenerative materials.
In France, several theatres, opera houses and festivals are demonstrating commitment to circularity and the use of regenerative materials, with support from the French Ministry of Culture.
Recognizing the significant volume of waste and greenhouse gas emissions generated by this arts sector, reusable sets are becoming more common. Theatres deploy disassembly practices and make thoughtful materials choices for both reuse and to address materials toxicity. Opera productions are exploring use of compressed cork to replace the use of polystyrene (a petrochemical material), and they also found the materials suitable for reuse.
The key message here is to consider the environmental impact of your materials before and after they are made and used, and to explore bio-based and regenerative materials.
Materials made from cork, bamboo, hemp and straw, for example, may be preferable to materials made from slower growing and non-sustainably managed forests, and they are much more environmentally advantageous to materials with high embodied carbon, made from extractive resources, such as metals and plastics. Use of regenerative and bio-based materials will significantly reduce the greenhouse gas emissions (GhGs) associated with your staged environments.
Visit Resources & Inspiration for articles on regenerative materials and regenerative building. If this is a topic of particular interest, you may want to dig deeper by reading books or taking courses on regenerative materials and regenerative design.
Museums commonly used vinyl PVC lettering, high pressure laminate panels (Embedded Phenolic Resin) and acrylics for their interpretive panels. These products made from petrochemicals are not recyclable, and they do not biodegrade. Some studies indicate that laminate panels may not break down for at least 1000 years. A particular issue with vinyl lettering is that a whole sheet is used to make the labels. Plastic-free adhesive wall lettering and signage exist, but are not commonly available.
These materials create a professional-looking presentation, making it difficult to convince colleagues to explore alternative non-toxic, biodegradable or recyclable materials. Some museums and galleries are using alternative didactics, such as hiring professionals to print or stencil directly on walls or on construction paper, cardboard or falconboard. Wheat paste and nori paste are two non-toxic glues for affixing interpretive panels to walls or objects, and there are a variety of non-toxic inks and paints available.
Falconboard is a fully recyclable rigid sheet that can substitute for plastic sheets. The Museum of Vancouver used this paper-based material (also called honeycomb cardboard) for their Reclaim+Repair exhibition didactics. For their Planetopia exhibition, the Museum of Communications in Bern, Switzerland went higher up the zero waste hierarchy. They found a local company that collects offcuts from various industry sectors, and used them to create signage from used materials. Waste cardboard boxes from Vespa motorbikes were turned into attractive wall didactics.
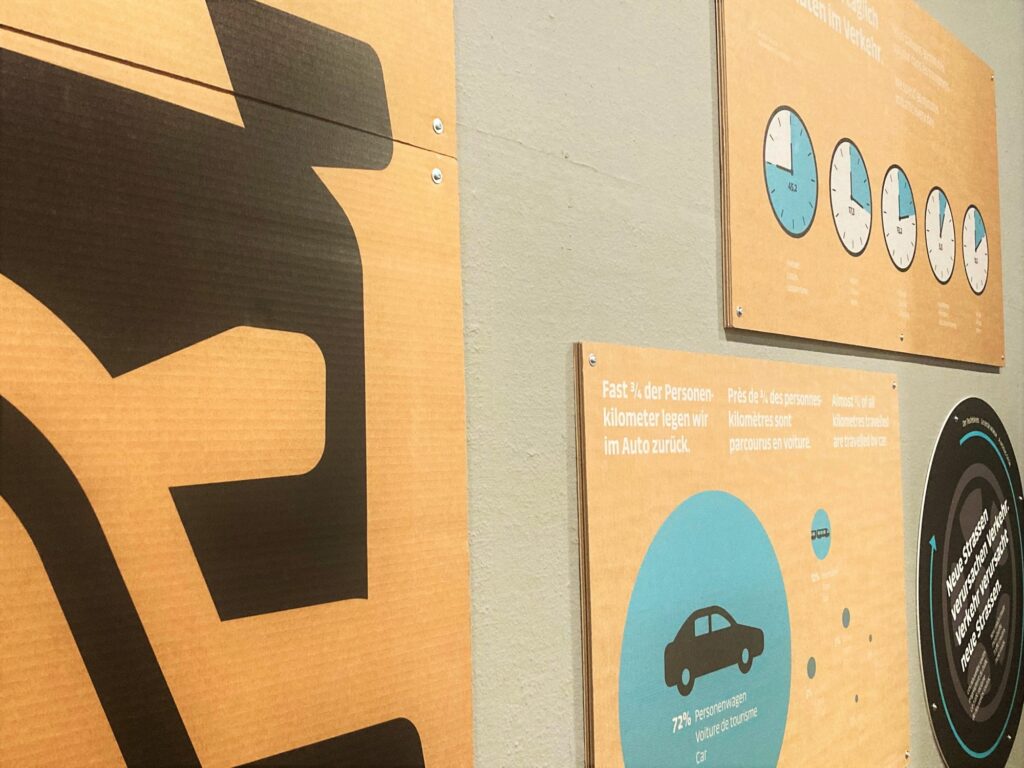
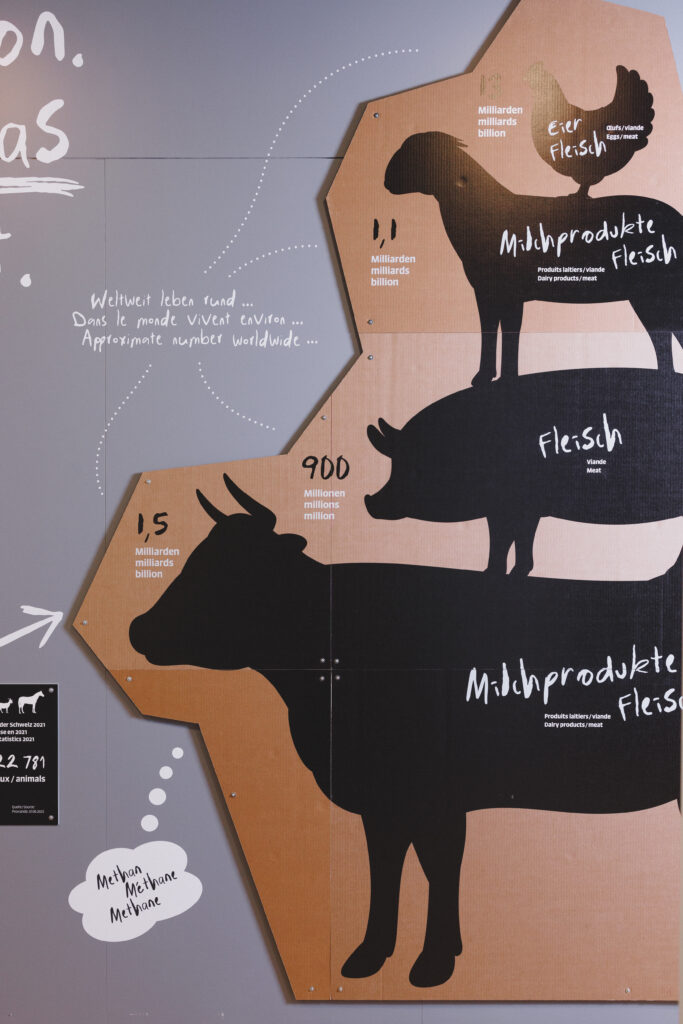
Certain materials choices may have long been favoured by designers and fabricators of theatre sets and exhibitions, but experimenting with alternative, low-carbon materials can be an exciting challenge. The scale of production of staged environments may be eclipsed by the volume of materials used in building real estate developments. However, the high turnover of staged environments results in significant use of materials. Choosing to use bio-based materials and materials with environmental certifications may add more to a project budget, but if circular principles of reuse, reduce and recirculate are deployed, these costs may be amortized over multiple productions.
Some questions to ask when selecting materials:
Durability: Are the materials durable and reusable many times, provided the design, construction, and deconstruction support an extended lifespan?
Embodied carbon: What is the global warming potential of the products and materials for its full lifecycle from sourcing of the raw materials to shipping, manufacture, use and end-of-life disposal.
Ecological footprint: Did the materials require extraction of the raw materials that negatively impact the environment. Look for third-party certification of wood materials made from sustainably managed forests. Visit the Glossary for some certifications.
Building wellness: Do the paints, MDF and other materials containing glues with volatile organic compounds (VOCs)? Off-gassing of VOC compromises air quality.
Case Example: Experimenting with Circularity to Guide Future Exhibitions
The Design Museum in London, applied circular principles for their Waste Age exhibition, using repurposed, upcycled and regenerative materials.
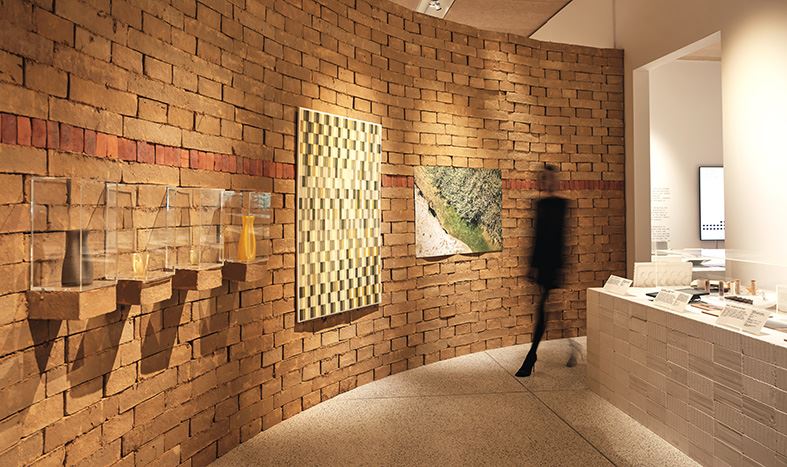
Case Example: Prioritizing Repurposing, Borrowing and Upcycling in Materials
The Museum of Vancouver (MOV) prioritize the application of circular principles and practices into planning and materials selection for their upcoming temporary exhibition Rain People.
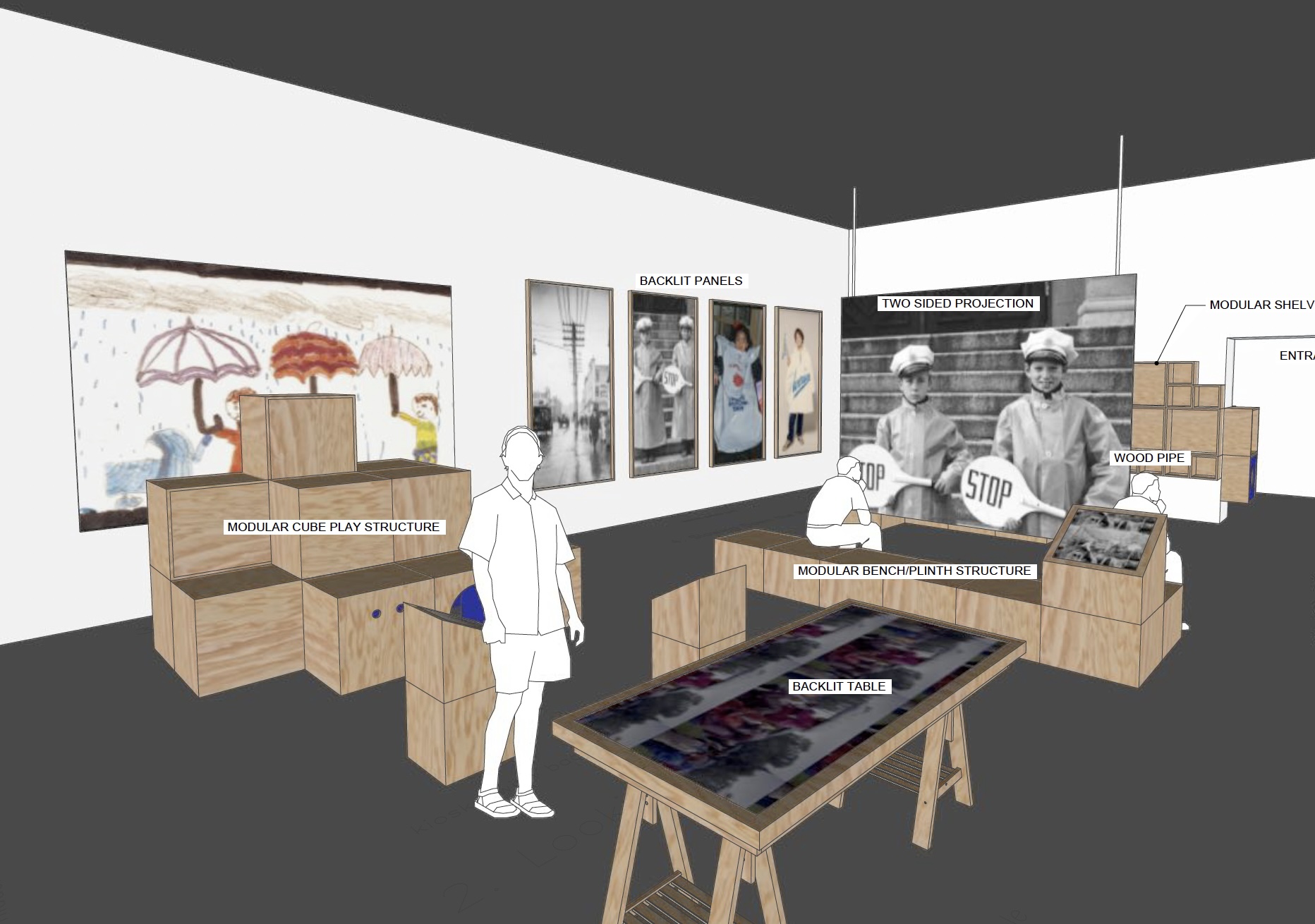
How we choose to build and assemble staged environments will impact the amount of waste we generate at the beginning and at the end of life of exhibitions and theatre productions.
Which of the 5Rs circularity principles are relevant to the construction of theatre sets and gallery or museum exhibitions, and how do we deploy them?
Definition Principles of Circularity (the 5Rs)
The principles of circularity are based on the idea of creating a regenerative economy that eliminates waste and pollution, keeps materials in use, and replenishes natural systems. The 5Rs circularity principles are: Re-think, Refuse, Reduce, Reuse, and Re-circulate. See Circularity.
For exhibitions and other staged environments, the SAGE toolkit focuses on the above five (5) key principles of circularity. The 5Rs guide planning, design, materials selection, building and disassembly of staged environments. There are additional “Rs” among circular principles, some more relevant to manufacturers or government waste management practices. See the 5 Elements: Planning for more detail.
Quick Tips
- Identify circular building techniques at the Planning and Design stages.
- Ensure fabricators are part of circular commitments including materials reuse.
- Best practices: Avoid glue and staples and use joinery when possible.
- Invest in reusable joinery, modular walls and other modular elements.
- Build to avoid offcuts and waste, and reuse offcuts where possible.
- Salvage and repurpose materials and elements (risers, walls, etc.) for reuse where possible.
- Budget time for circular building (and unbuilding) practices.
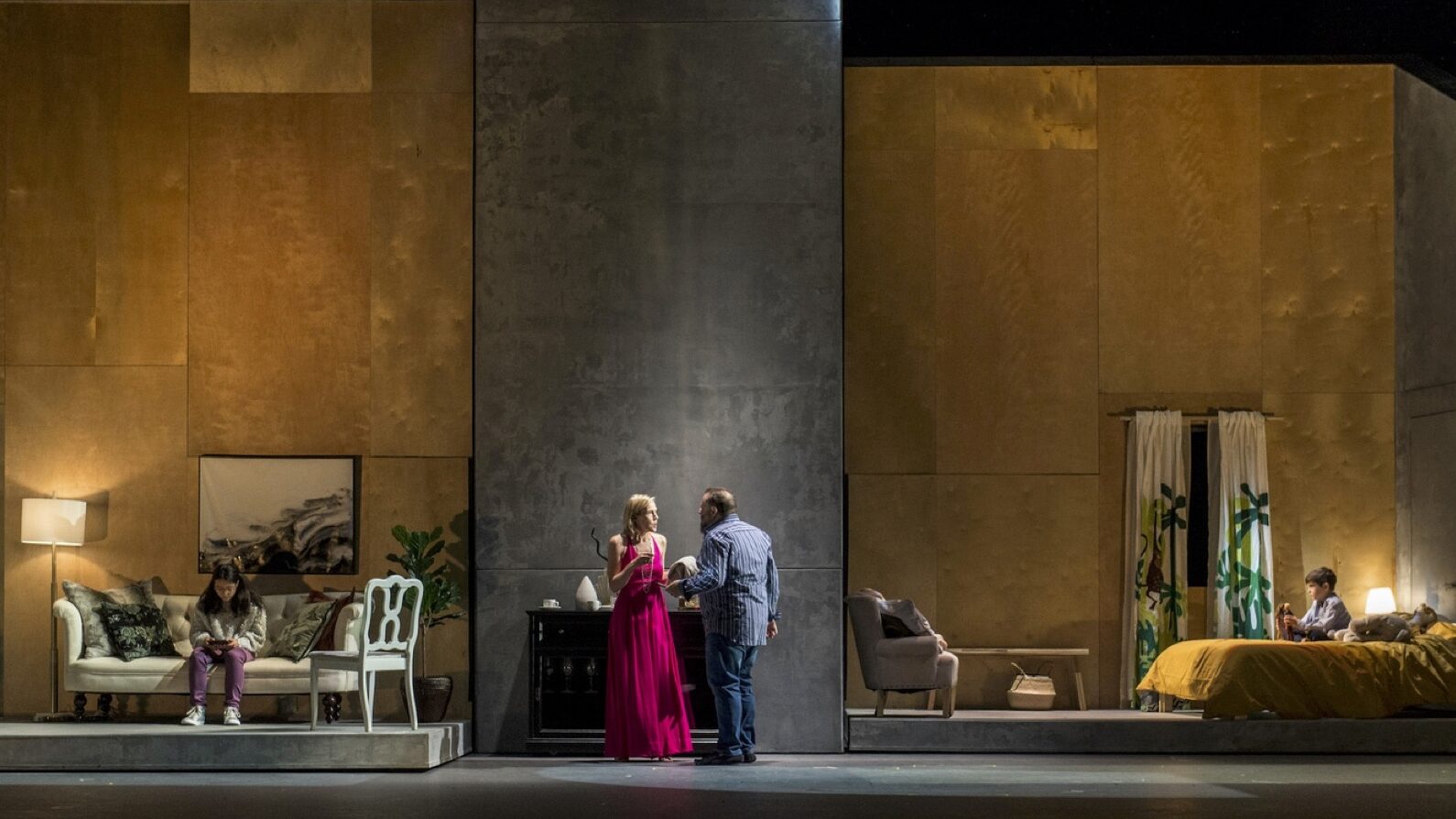
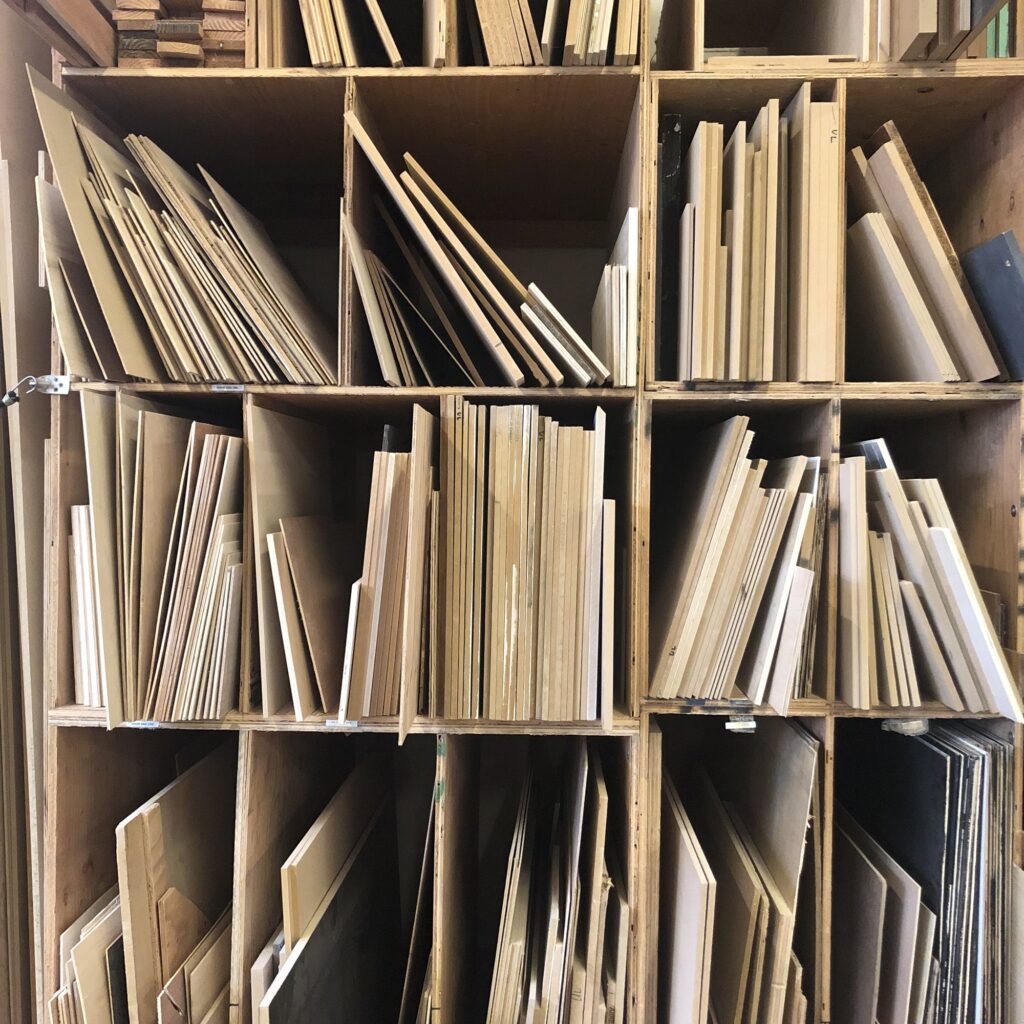

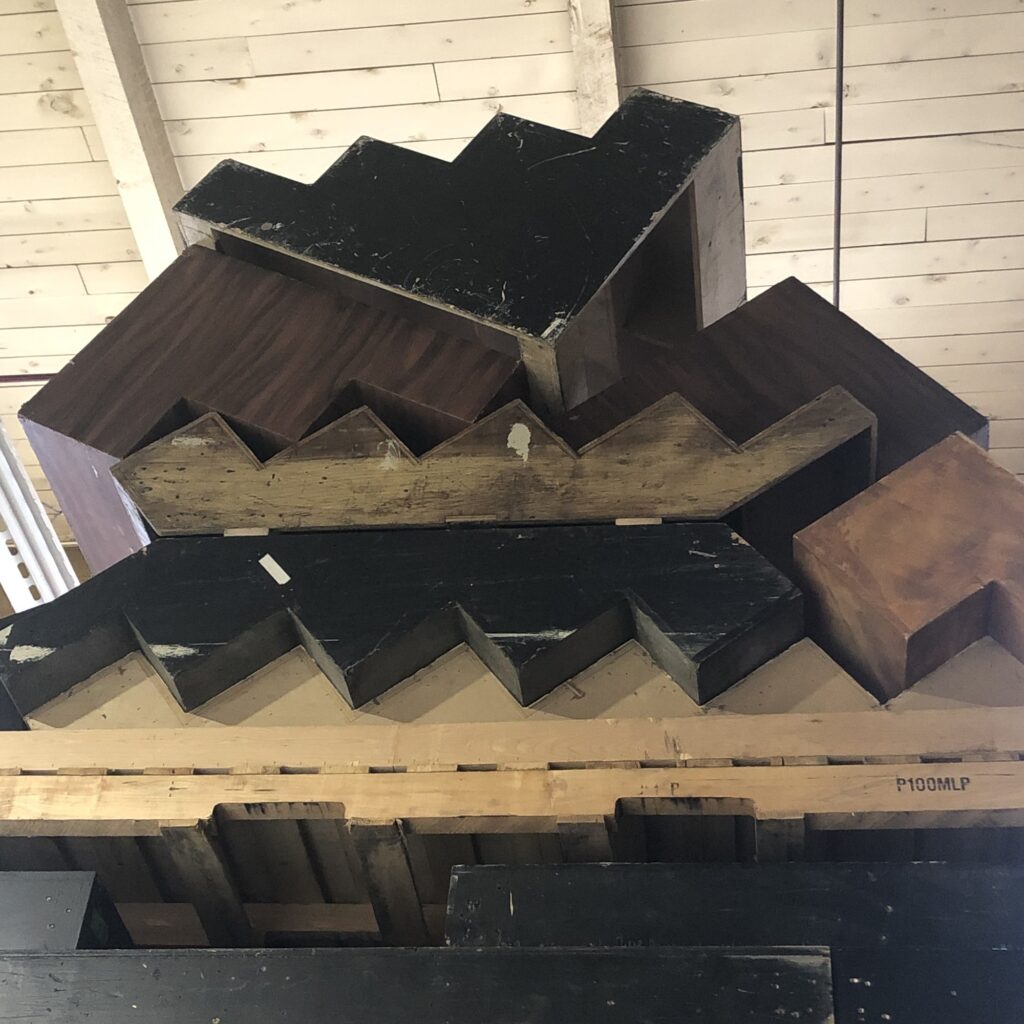
How to Integrate Circularity into Building Staged Environments
Here are key considerations and techniques that support circular construction.
Planning and Design influence and often control how to build staged environments. Circular construction options may be limited if not factored into planning and design early in the project.
Share circular goals with project fabricators early to get their ideas for assembly (and disassembly) techniques and joinery that will enable materials reused and reclamation. Ensure fabricators are aware of your commitment to minimizing offcuts and unnecessary construction waste. Listen to their ideas or concerns about functionality, safety, costs or time and techniques.
Tip: Include circular commitments in bid documents and RFPs for contract fabricators and co-create or share the Project Pledge if you’ve taken it.
Template Language for Bid Documents
We have created sample language for for how to include circular commitments in bid documents and RFPs for contract fabricators.
While the structural components of most exhibitions will use conventional materials, such as lumber and panelling, can the design and fabrication team advance circularity through creative use of unconventional used materials or more innovative ‘green’ materials?
Case Example: Reuse of Unconventional Materials in Staged Environments
The stage production, Winslow, by the theatre and company L’Escaouette, in Moncton New Brunswick, featured a large screen made from locally-sourced repurposed fishing cables and ropes.
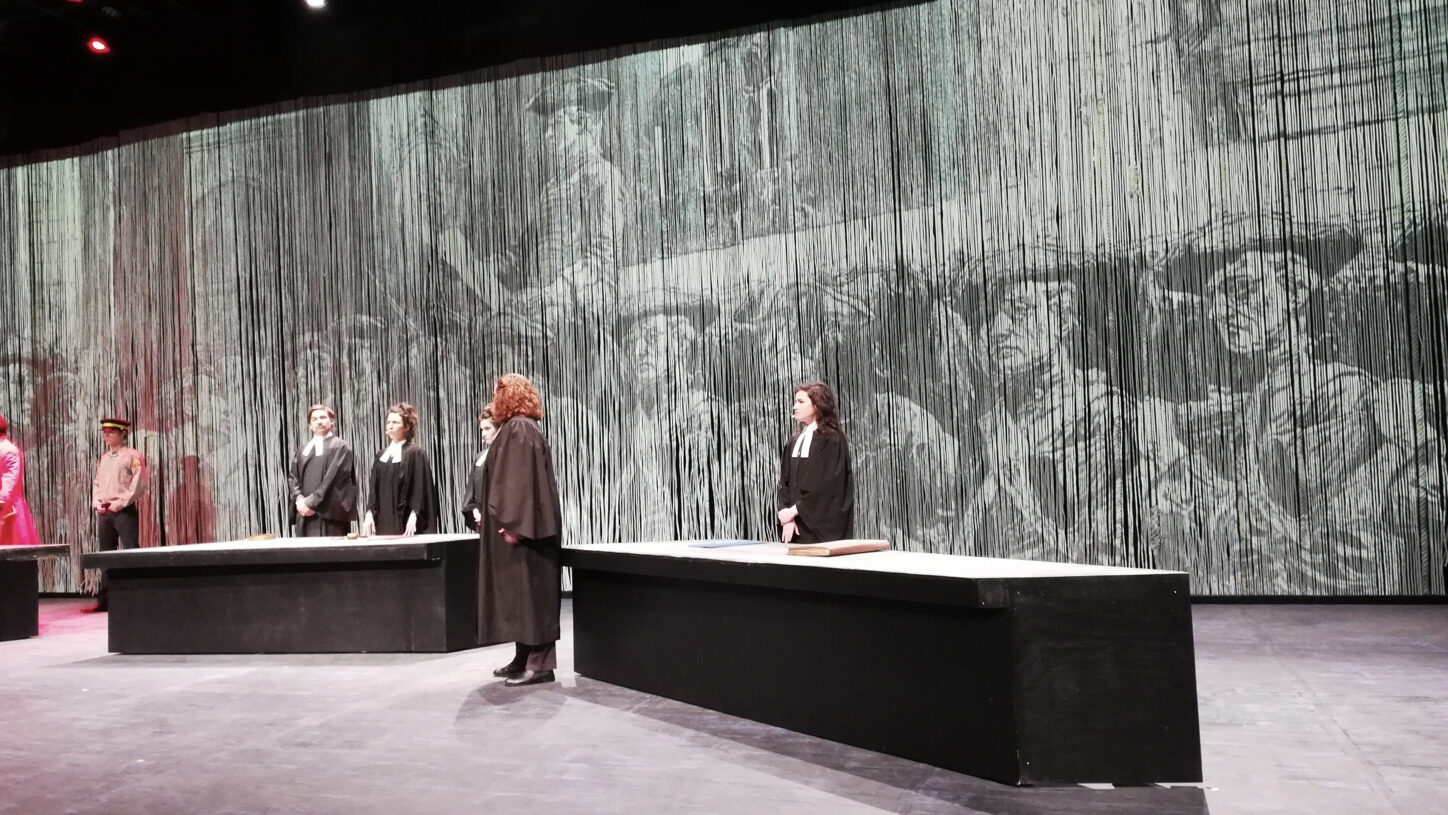
Your fabricators lead the work of disassembling end-of-life staged environments to make way for the next exhibition or theatre production. Ensure fabricators are trained and tasked with unbuilding to preserve materials for reuse, and materials identified for use in upcoming exhibitions or stored or shared for future.
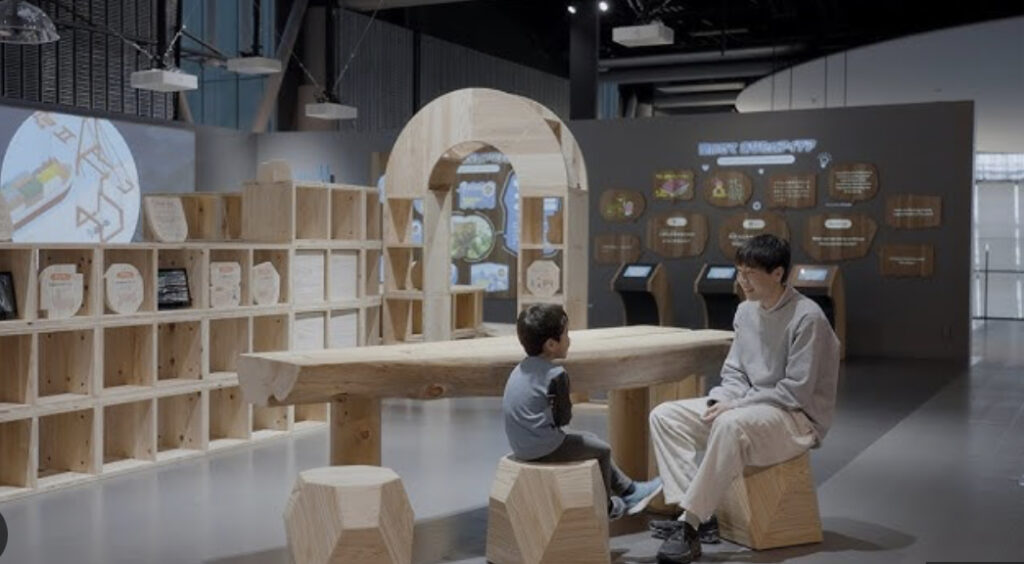
Ensure fabricators know how to build-for-disassembly or how to adapt configurations of modular systems. Design specification may indicate use of tongue-and-groove, intersecting slots or other joinery assembly techniques, but the temptation may exist for fabricators to add glue for stability to the joints. Sometimes this is necessary, and sometimes it is just a habit.
It should also be noted that assembly techniques like the use of pegs or tongue-and-groove require skilled fabricators and may take additional time for construction. Project planning should account for this by budgeting sufficient time for fabricators to employ these techniques that enable disassembly and materials reused.
Biscuits or domino joinery is an efficient technique providing a strong, reliable bond while offering quick assembly and greater flexibility for future disassembly and reuse than some other assembly techniques.
Glue and staples make a strong, permanent bond, which makes disassembly difficult and potentially damaging to the materials. If you must use glue to strengthen or stabilize joints, pair it with brad nails instead. Brad nails offer a similarly strong hold but are much easier to remove without damaging the materials.
Establish a policy to minimize use of glue and staples. Encourage use of screws or other reusable joinery instead of nails. You may still be able to reuse panelling and lumber if assembled with glue and staples, but you will likely need to trim the wood to cut out these parts. So there will be some offcuts that are not reusable.
Fabricator Josh Doherty (Museum of Vancouver and UBC Museum of Anthropology) avoids glue and staples. For looser joints, such as slot design (see image below), he uses pegs to tighten joints that loosened up with repeat assembly and disassembly. The Museum Ostwall in Dortmund, Germany, used strapping to secure and stabilize the modular system they used for their FLUX exhibition. See photo below.
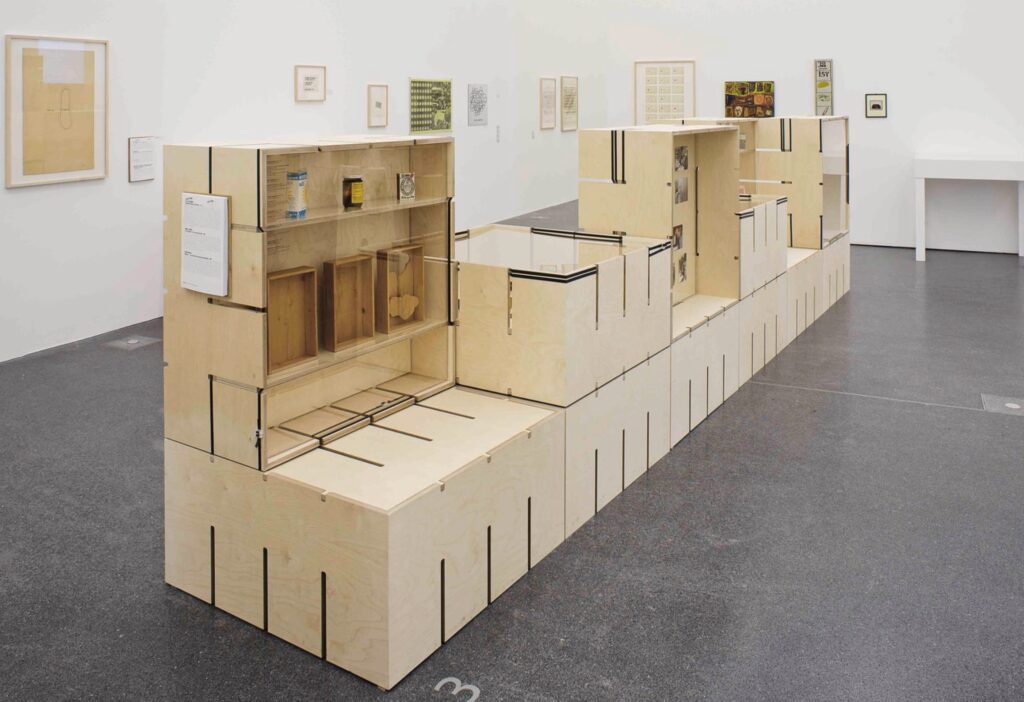
Types of Reusable Joinery
Various types of joinery allow for easy disassembly and reuse—here are a few examples.
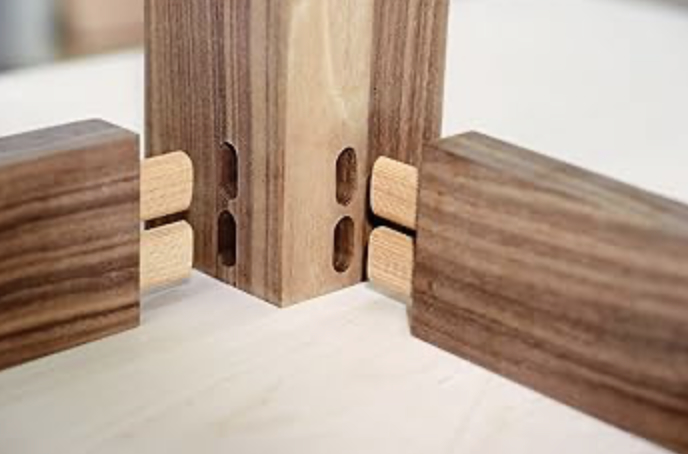
When offcuts occur, consider whether they are large enough to salvage and repurpose for use for didactics or other purposes in your project or others?
Save larger pieces of lumber and panels, and elements you build for reuse or repurposing when possible, or offer them to other arts organizations for reuse. If materials are too small, too damaged, ensure fabricators divert materials for recycling. While this is less desirable than reuse or repurposing materials, it is important to send waste materials to recyclers, not to landfill.
Plan ahead – before building and unbuilding, use Barder.art to search for used materials and elements for staged environments, and post materials that you will make available for sale, to lend or giveaway.
If you design and build your own modular systems or purchase modular units, such as Mila® wall systems, there is an upfront cost. However, that cost will be amortized over the long term use of the modular systems.
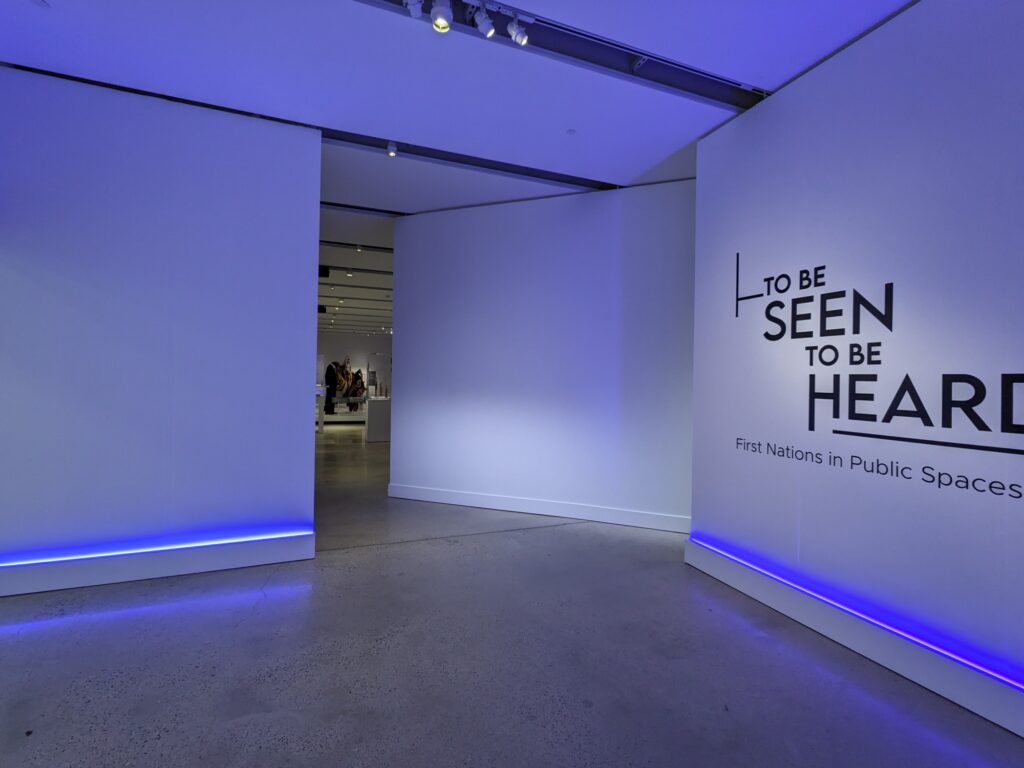
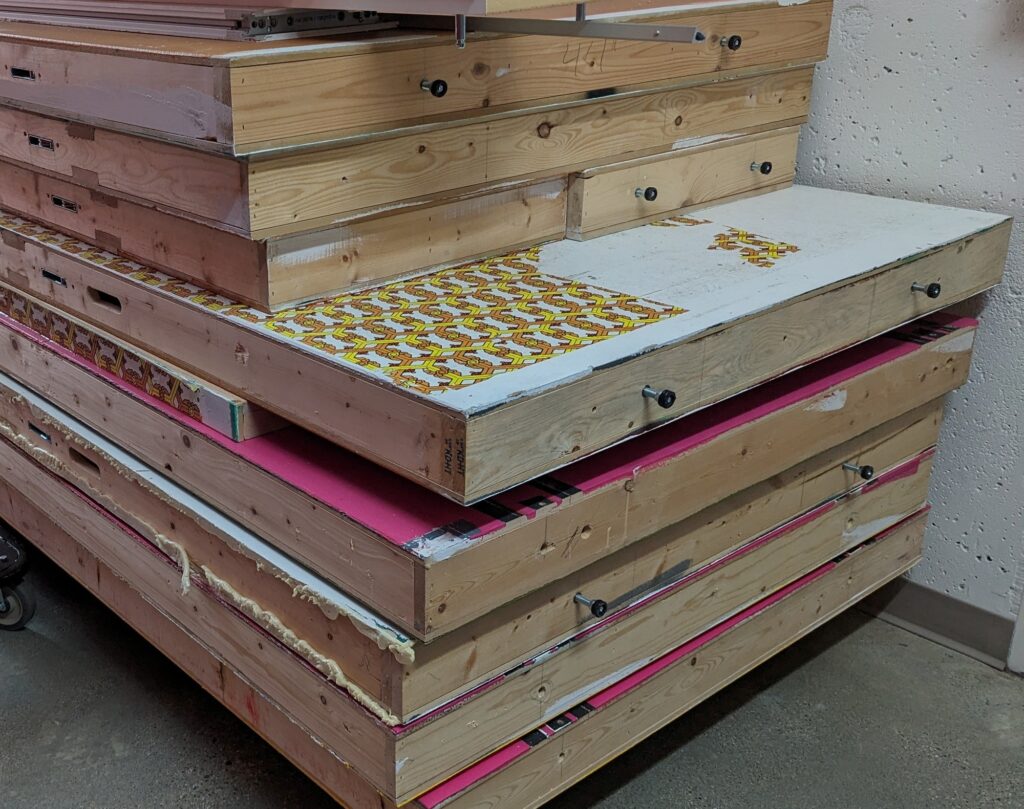
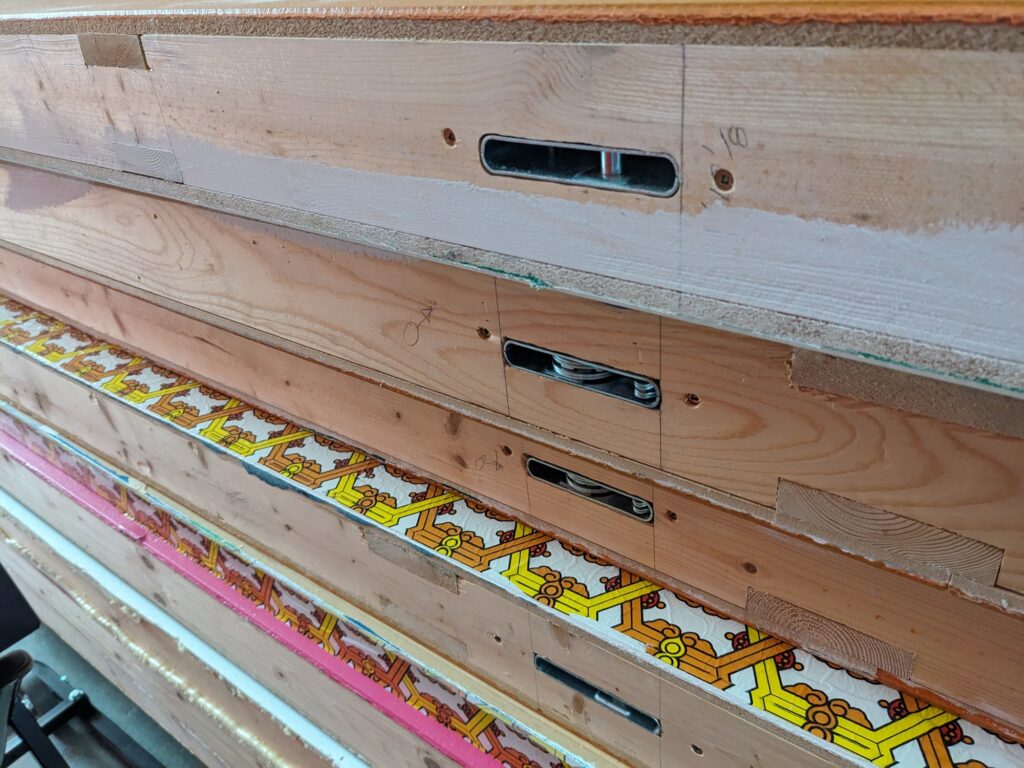
One important challenge to overcome is budgeting sufficient time for fabricators to deploy circular techniques for construction. Recognize that modular designs, design for adaptability, and design for disassembly will likely take more time to build the first time. However, they enable components to serve multiple purposes or multiple uses over time without compromising their integrity.
When time is constrained, fabricators may take short-cuts that compromise circularity. Planning, designing and fabricating should consider how to extend the life of materials beyond one exhibition or theatre production.
Case Example: Reuse of Unconventional Materials in Staged Environments
The stage production, Winslow, by the theatre and company L’Escaouette, in Moncton New Brunswick, featured a large screen made from locally-sourced repurposed fishing cables and ropes.
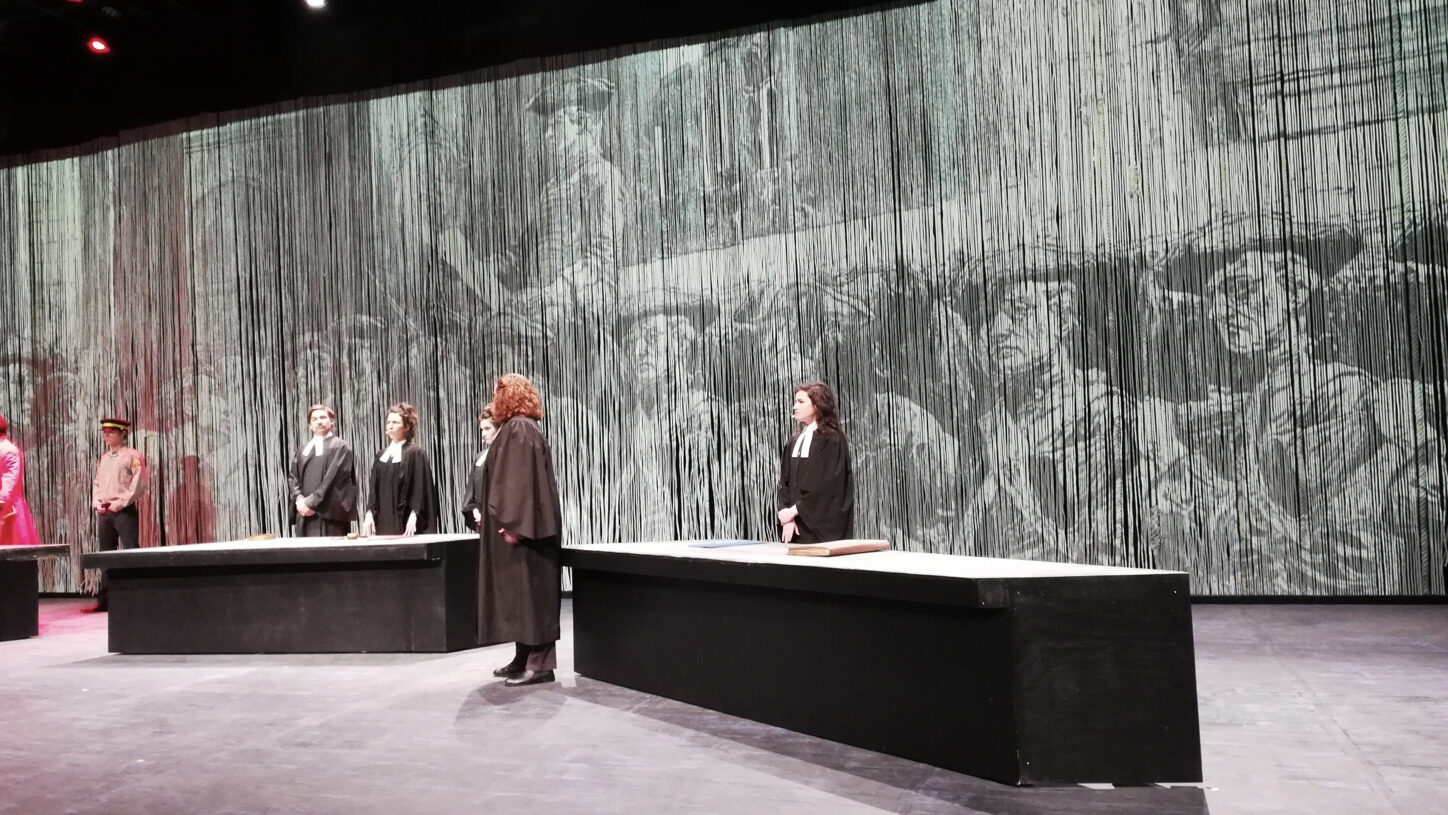
Case Example: Thoughtful Design and Building to Minimize Wood Waste
The National Museum of Emerging Science and Innovation in Tokyo, Japan set a goal to create an entire exhibition using locally sourced wood with minimal waste
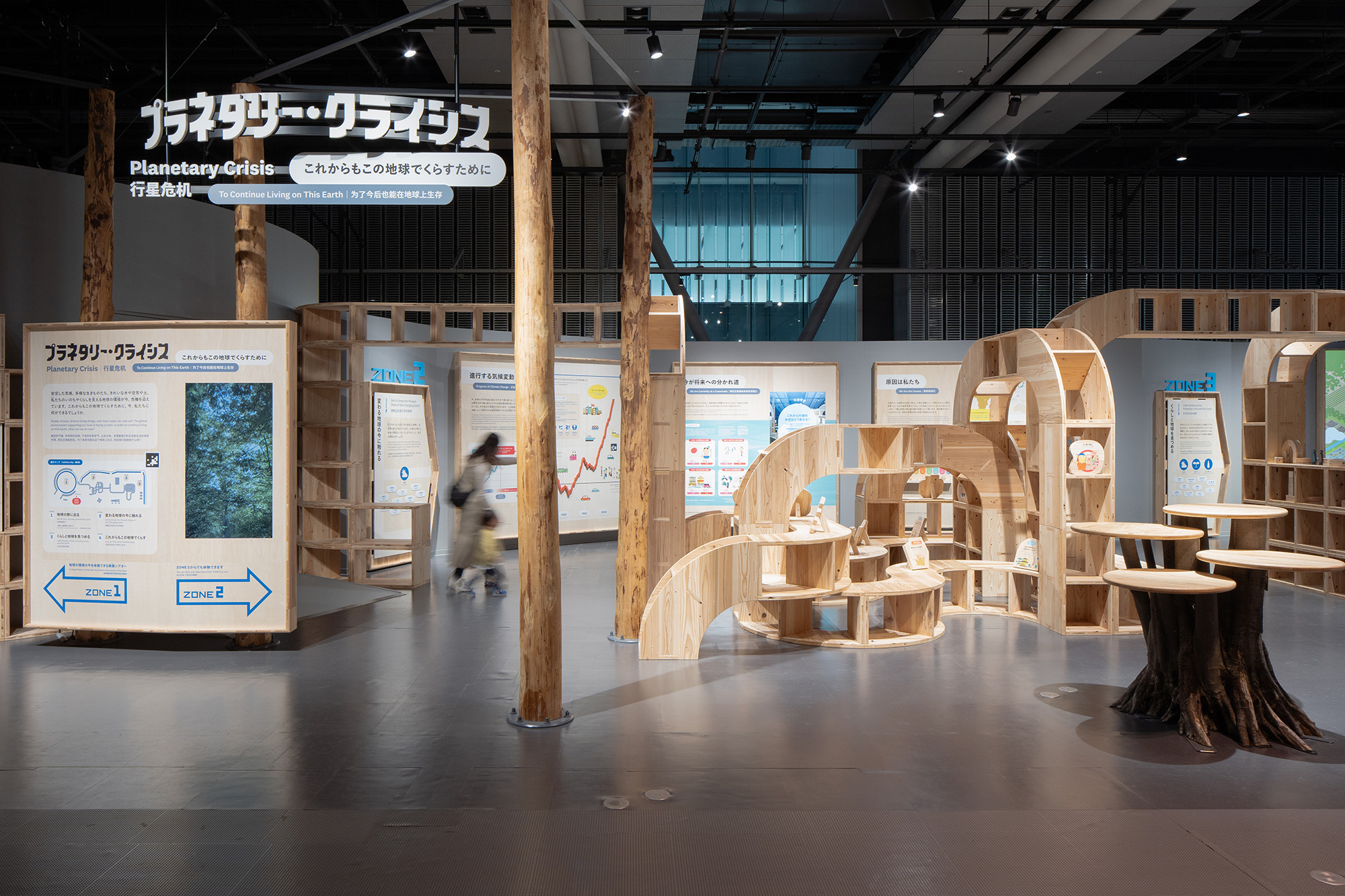
Unbuilding or de-construction provides another opportunity to apply circular principles in the cycle of staged environments.
At the end of life of staged environments, the focus is often on tearing them down as quickly as possible to make way for the next production. Yet, without commitment to unbuilding, organizations will limit their progress towards zero waste.
Some of the options for avoiding waste at the end of productions are dictated by decisions made earlier in the project. Did project planning allocate time and budget for unbuilding instead of demolition? Did the design of the theatre set or exhibition prioritize use of modular systems or structures designed-for-disassembly? Were durable materials selected that are appropriate for reuse in future staged events? Did fabricators build the theatre set or exhibition structure in such a way as to enable unbuilding?
Beyond these decision points, how can we rethink disassembly of staged environments to achieve zero waste or come closer to it?
Definition Zero Waste
Designing and managing products and processes to avoid and eliminate waste, and conserve and recover resources. Zero waste is an outcome of circular practices. See also: Zero Waste Hierarchy under “When You Must, Recycle”.
Quick Tips
- Establish unbuilding policies and procedures.
- Plan times and resources for unbuilding.
- Plan for storage or materials sharing for reuse.
- Create a materials inventory and update it when unbuilding.
- Train fabricators to disassemble items to preserve materials for reuse.
- Establish a sorting methodology.
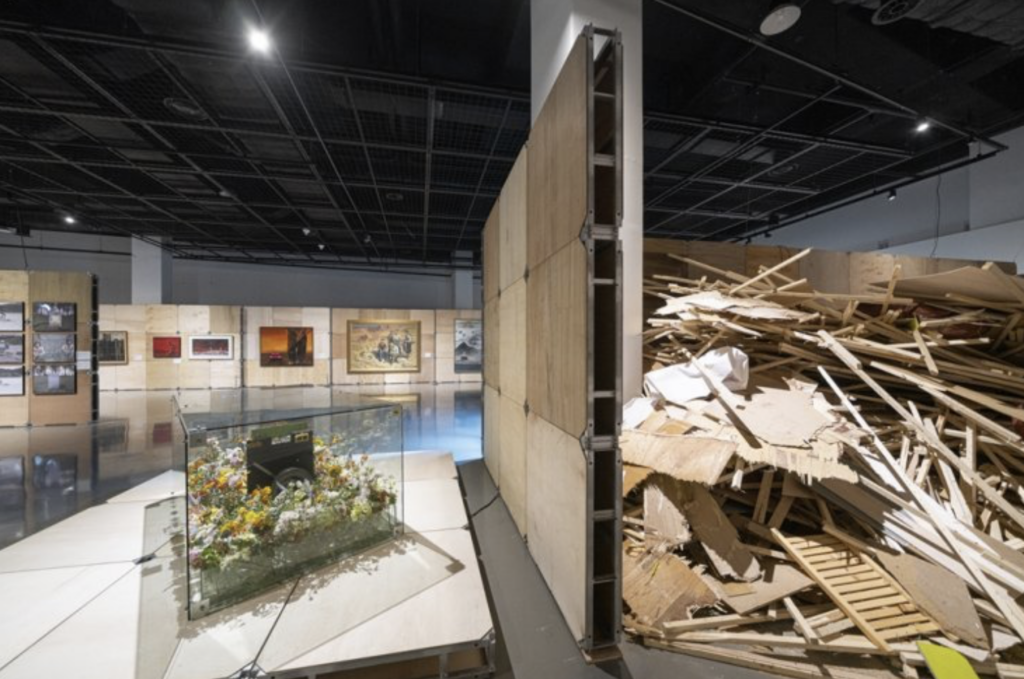
How to Integrate Circularity into Unbuilding Staged Environments
Unbuilding is probably the least interesting part of development of staged environments. Planning, design and building exhibitions and other staged events invites creativity. Unbuilding is mostly a mechanical and (if done well) a methodical process. However, it is a critical element of circular development and management of stage environments.
Here are key factors for successful unbuilding:
Elevating the importance of this element of circular production will be a significant driver toward zero waste. It will contribute to opportunities for extending the life of materials for reuse and repurposing. Establishing and socializing both an unbuilding policy and guidelines or procedures for deconstruction will increase the team’s commitment to unbuilding.
It is challenging to unbuild if you did not plan for it. Be sure unbuilding is integrated in the project plan, and sufficient time and resources are allocated to enable successful deconstruction. Lack of sufficient time and resources for disassembly will likely result in wasteful practices.
If you wait until disassembly to determine the next life for the materials and structures, it is probably too late. Plan ahead and schedule a review of the materials and structures. Which of them may be re-deployed in one of your upcoming exhibitions or theatre productions? If you do not need them, can you sell, lend or give away the materials?
Use online materials trading platforms like Barder.art-BC for posting materials, props and structures that will become available when you unbuild your production. Plant ahead and post weeks or months before the end of your production – so you are ready to redistribute them upon disassembly.
The Barder.art-BC online tool for the arts sector allows you to post the timelines for when your materials will be available. It also offers the option to lend materials instead of selling or giving them away. For their Dressed for History: Why Costume Collections Matter exhibition, the Museum of Vancouver searched for heavy draperies to borrow or buy second-hand. The UBC Museum of Anthropology obliged, lending the draperies to MOV for two years.
If there is no demand for your materials in your arts community at the time of disassembly of your exhibition or production, can you donate them to local charitable organizations, schools or post on general online marketplace like Facebook Marketplace? Metro Vancouver theatres, galleries and museums, check out the SAGE Directory of local organizations that accept donations of used props and other goods and materials.
A note on demand: Given the high volume of used wood coming from deconstruction of homes in Metro Vancouver, it is unlikely you’ll get much demand for used wood from your staged environments. UrbanJacks accepts used lumber, but only from partners that are also purchasing their upcycled lumber.
Specify deconstruction (not demolition) in bid documents and contracts with external project teams, and include it in your Project Pledge.
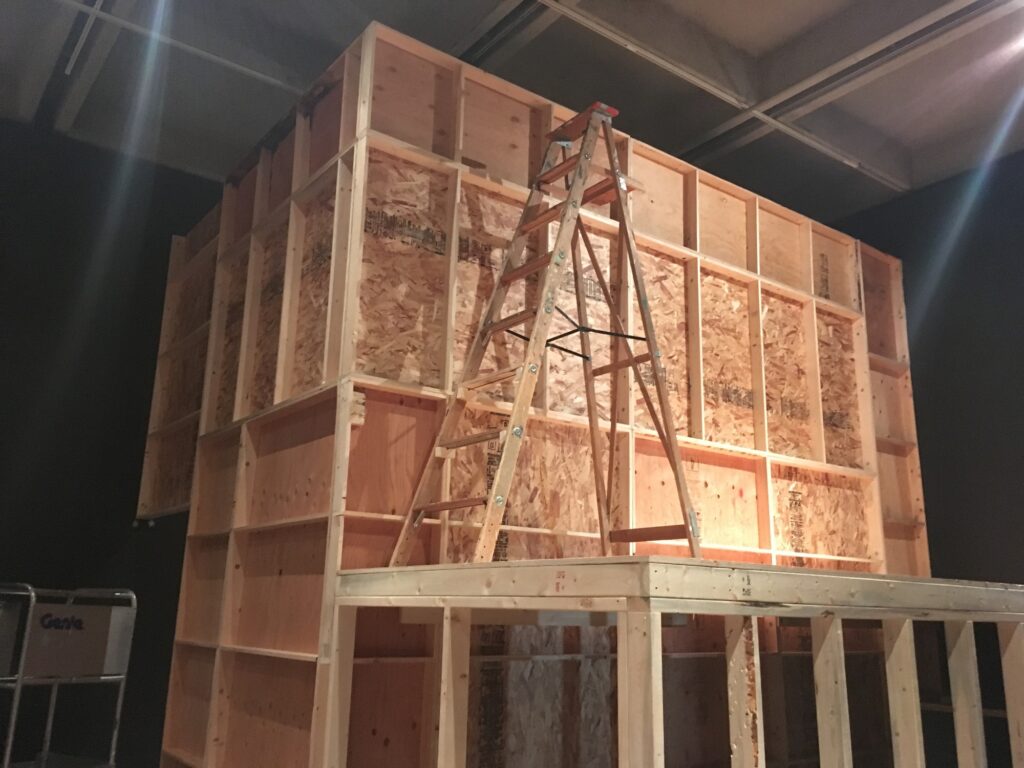
If you are expanding your use of modular walls and structures, and plan to store materials that do not have immediate reuse, do you have space for them? Space is sometimes identified as a reason for limited reuse of materials. Planning ahead and a good inventory system should alleviate some of the storage demands as materials may be kept in better circulation.
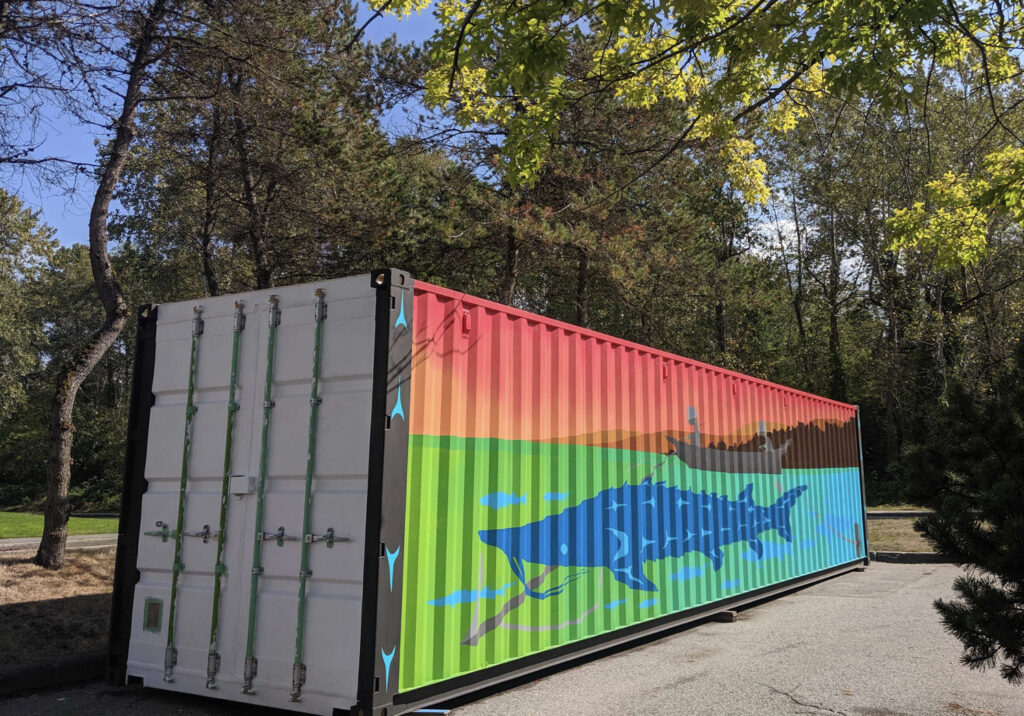
The Museum of Vancouver uses a shipping container for additional storage in order to save materials for reuse.
The Museum hired Stó:lō artist Dean Harris to paint the container on 5-sides (including the top for aerial views) to make it an art piece as well as functional storage. Space was allocated in the nearby parking lot for the storage container.
Before planning any purchases, the project team reviews materials in storage in order to consider them for reuse in upcoming exhibitions.
Ensure the fabricators’ duties include taking inventory of materials disassembled. If the materials are posted to Barder.art or another online marketplace, they will require images with descriptions and notes on quantity.
If you are storing for reuse, developing a digital inventory of available materials and structures will be an efficient way to review available materials when you plan new productions. Science World keeps a digital inventory of all their display cases with graphics and information showing sizes, shapes and configurations.
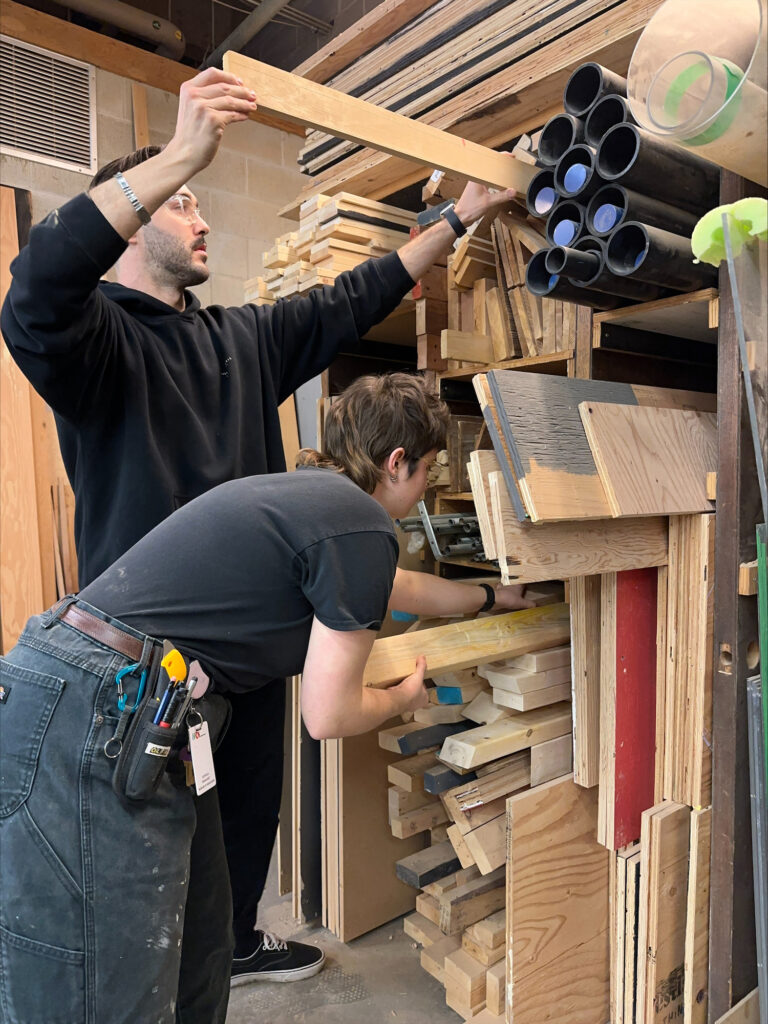
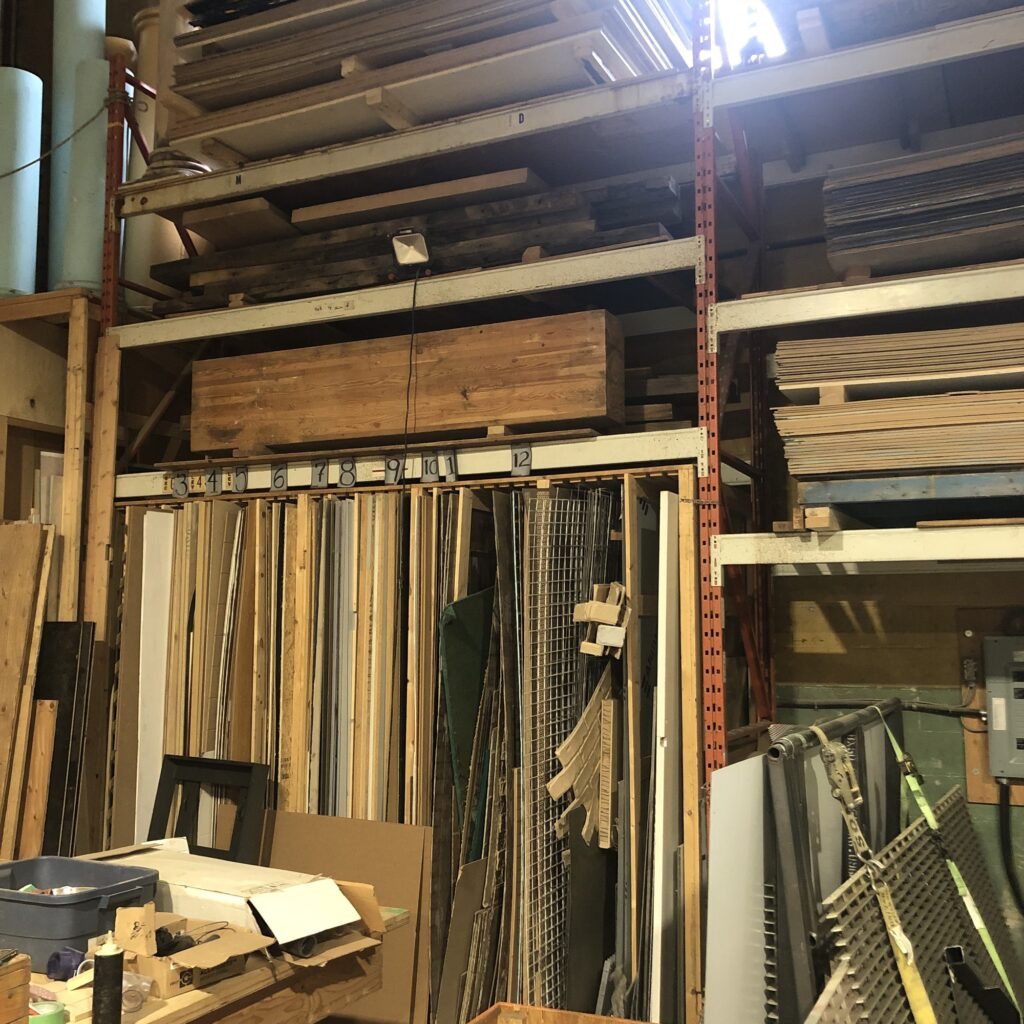
Ensure fabricators are trained and tasked to disassemble structures in a way that optimizes the size and condition of materials, preserving them for reuse. Understanding the process of taking things apart thoughtfully and carefully can reveal new ways to repurpose materials, improve efficiency, and ensure that every piece has value for future use.
The joinery you used will influence your deconstruction method. Are you able to disassemble structures and materials in their entirety, or did the assembly use glue or other techniques that may require that you trim or cut panels or lumber to separate them?
Sorting as you deconstruct will save time and ease the inventory process later. Set up a deconstruction staging area with designated piles for each type of material.
Pile all 2x4s in one spot, keeping them separate from other piles of 1x2s, plywood panels, MDF, and other materials you want to reuse. Be sure to record the materials in your inventory if you are storing them.
Materials for recycling or disposal should be put in other separate piles. If you are tracking your greenhouse gas (GhG) inventory, you will want to know the weight of materials you send to landfill.
You may also want to track the materials you save or divert for reuse and report on the avoided green GhG emissions associated with materials diverted from landfill for reuse. You could estimate based on the board feet of lumber, etc., or if you’re serious about tracking your avoided waste (and avoided GhG emissions), purchase reusable mega bags or bulk bags to put materials in to weigh, and an industrial portable weight scale.
Arts Commit created Climate Impact Reports (CIR). This is a free online tool to enable arts organizations to track and self-report on their circular actions, waste and waste diversion and other sources of greenhouse gas emissions. The Materials Afterlife Checklist in CIR is a useful template for compiling data on the materials removed at the end of life of exhibitions and recording what you did with them. Categories include: reused –for the same type of use; repurposed –used again but for a different type of use; recycled (collected for recycling); composted; and sent to landfill. Artists Commit’s goal is to provide project teams a simple tool to track key areas of climate impact, and to promote transparency within the sector in addressing the climate crisis. You can see reports from arts organizations worldwide and compare your organization to theirs.
If materials are too damaged or too small to be considered for reuse or repurposing, recycling or composting may be an option. These are lower down the zero waste hierarchy but still preferable to sending materials to landfill. If you are in a larger urban centre, with a bit of research you may discover options for recycling a broader range of materials than what your municipal government handles. There are private companies collecting used drywall to remanufacture into new drywall and other gypsum products, and companies that recycle Styrofoam and other materials.
Definition Zero Waste
Designing and managing products and processes to avoid and eliminate waste, and conserve and recover resources. Zero waste is an outcome of circular practices. See also: Zero Waste Hierarchy under “When You Must, Recycle”.
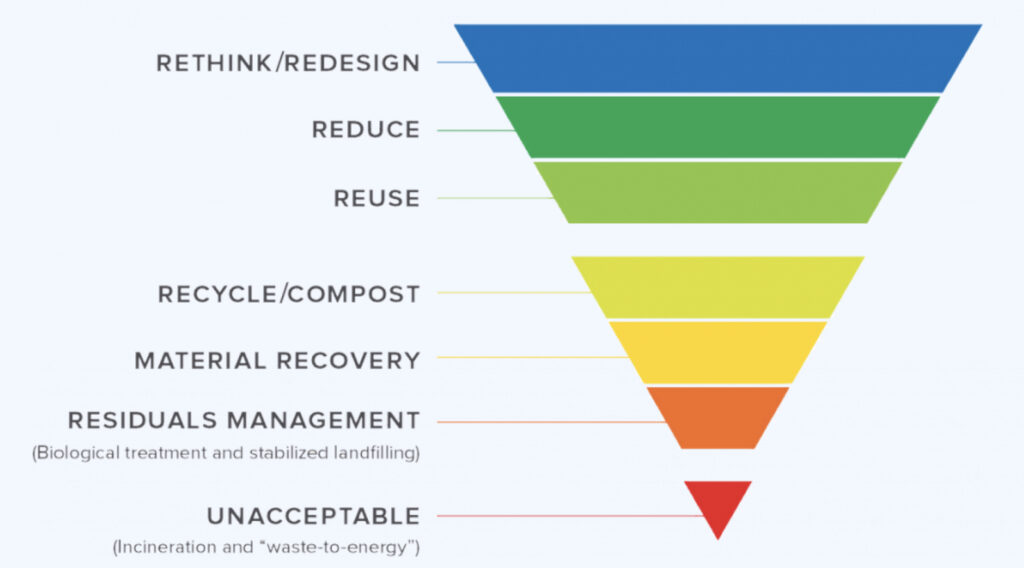
Case Example: Planning for Disassembly and Repurposing
MoMA’s exhibition, Adam Pendleton: Who Is Queen? made a bold statement with tall scaffolding holding the artist’s works. The structure made to resemble metal was built from wood and painted black, and was carefully disassembled at the exhibition’s close to allow for material reuse.
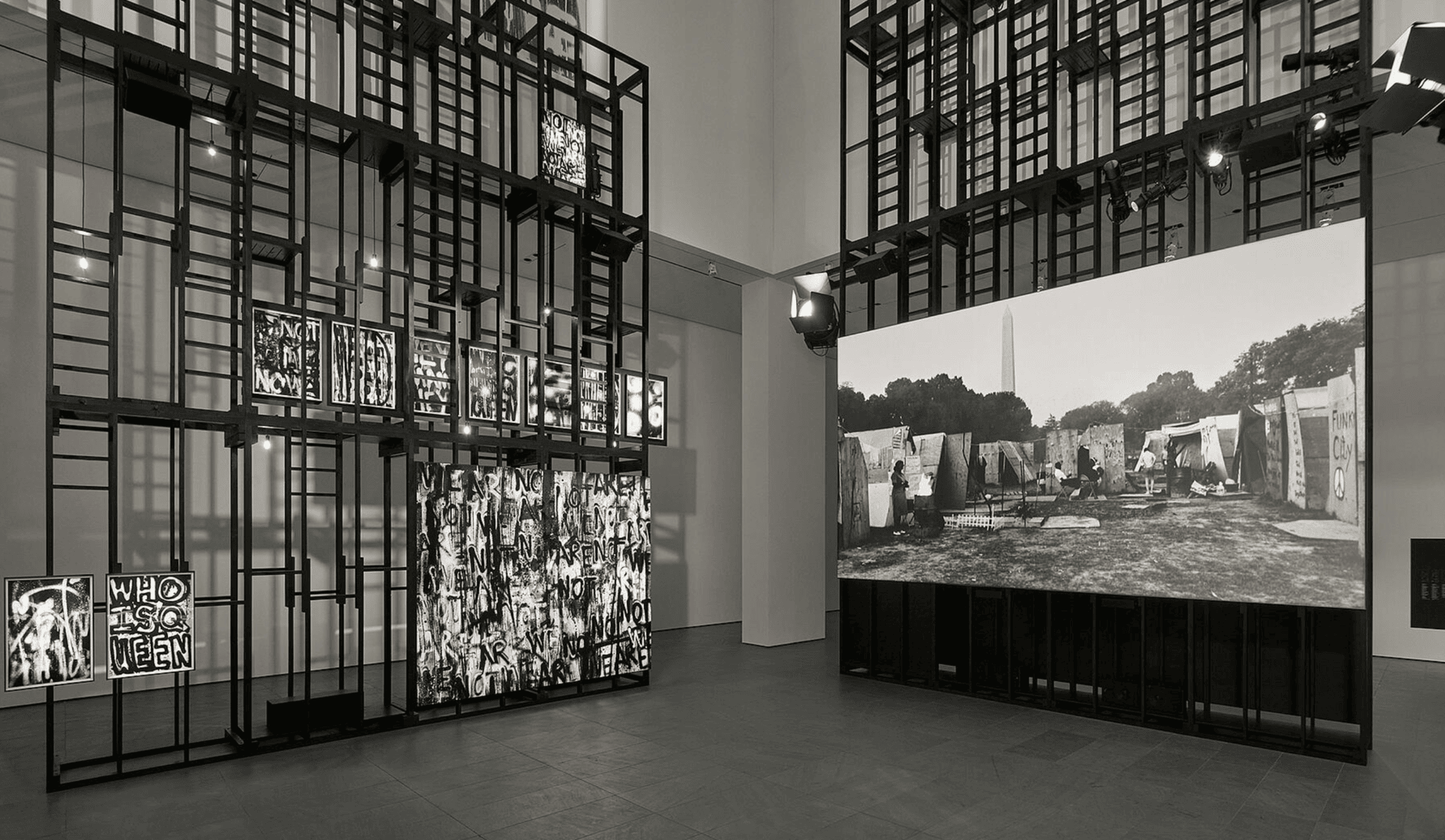