Case Example: Thoughtful Design and Building to Minimize Wood Waste
Planetary Crisis – To Continue Living on this Earth
National Museum of Emerging Science and Innovation
Tokyo, Japan
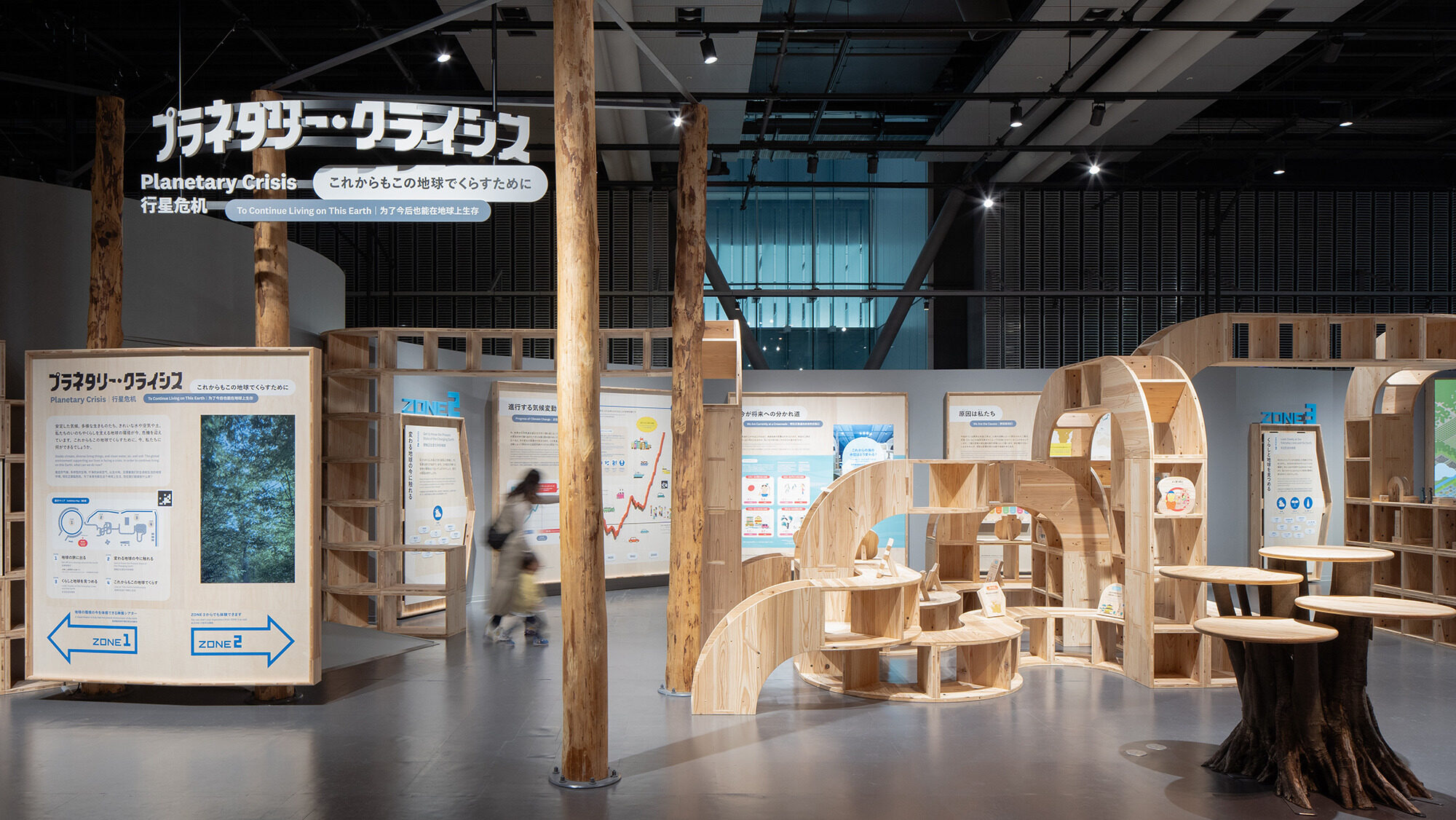
For one of their permanent exhibitions, Planetary Crisis – To Continue Living on This Earth, the National Museum of Emerging Science and Innovation in Tokyo, Japan set a goal to create the entire exhibition using locally sourced wood as the main material and designing and building to minimize negative environmental impacts of the exhibition.
First, the lumber was sourced from thinning forests—not clear cut – to support sustainable forestry management practices in Japan. The exhibition used 10m3 of domestic wood and lumber, and they calculate that about 6,000 kg C02 of carbon is stored in the wood.
Much of the focus was on maximizing use of the new materials and minimizing waste through modular design and thoughtful use of offcuts. Exhibition design includes modular elements which were assembled using mortise and tenon (similar to tongue-and-groove). In Japan, woodworking has a long history of craftsmanship using assembly techniques cut from the wood, and the fabricators for this exhibition adopted those skills to avoid the need for metal fasteners or adhesives.
The centre of the large exhibition space was designed with two sets of curvilinear modular design elements in different shapes. They were designed and built for multiple functions: placement of exhibits, seating space for visitors, and entrance gates to exhibition areas. The modular design and assembly systems enables reconfiguration to accommodate visitor flow and positioning of exhibits.
The project team collaborated with an architecture firm to design in 3D and cut the wood pieces digitally. Given the curvilinear design, they anticipated waste spaces in the dimensional lumber, so they laid-out the patterns of wood pieces and reviewed the layout before cutting was done. The goal was to lay-out the patterns to minimize waste from offcuts. They also considered the size of offcuts and how to repurpose them.
This approach differs from handing over a design to fabricators. This allowed time for adjustments before cutting, and it enabled the team to come up with ways to make effective use of the wood and the scraps.
Some plywood offcuts were stacked to make table legs, and hollowed-out shapes were used as the base of sign boards.
Other scrap wood (offcuts) was used for interpretive panels. Recognizing that didactics often contribute to negative environmental impacts of exhibitions, the project team chose to avoid use of vinyl letters and adhesives or printed vinyl sheeting which is discarded when exhibitions end. Didactics were painted or printed directly onto (offcut) wood panels, and other didactics were projected digitally onto larger wood panels and tables.
The design team worked with an architecture firm to build a modular display system and reduce waste. They were able to digitally visualize the wood cut pieces during the production phase. They optimized the waste spaces between the curvilinear pieces to cut the didactics.
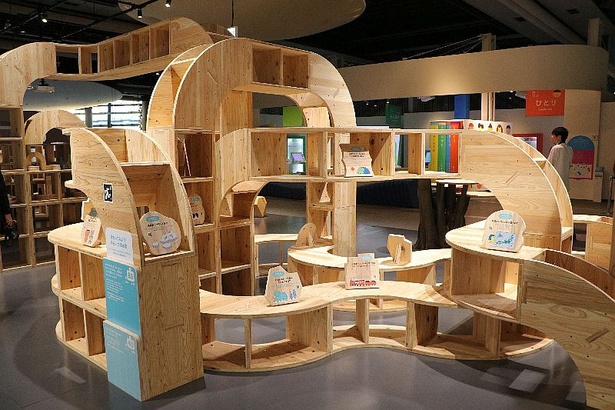
The museum shared their waste reduction and environmental efforts with visitors, and they conducted workshops about materials re-use. Fabricators made miniature replicas of the furniture and other exhibition elements for educators to use as teaching aids for students and other visitors exploring concepts such as modular design.
Thoughtful and collaborative design and construction of this exhibition resulted in 60% reduction in waste and an estimated 3000 kg of avoided greenhouse gas emissions by minimizing materials disposal. According to Project Manager, Yamada Chiharu, assembling a diverse team to collaborate on planning, design, materials section and construction, was critical to achieving their environmental goals. The team’s innovation and flexibility, including their willingness to adapt ideas and plans based on collective input, also played a significant role in the project’s success.