Case Example: Rethinking the Planning Process to Maximise Materials Reuse
Planetopia exhibition
Museum of Communication
Bern, Switzerland
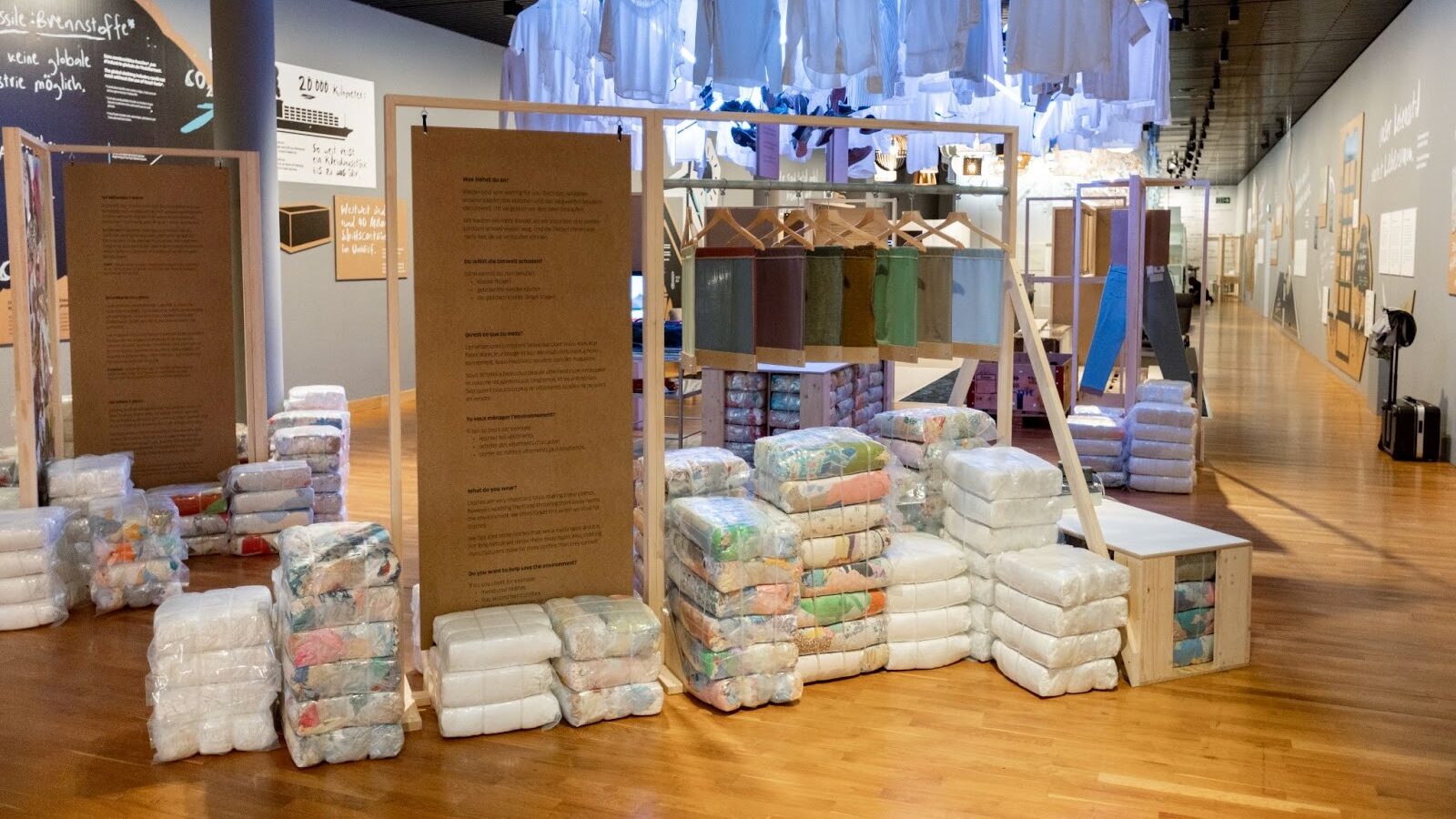
The Museum of Communication in Bern, Switzerland developed an exhibition titled Planetopia. The exhibition’s theme, centered on consumption and its environmental impacts, inspired the museum to take a broader look at the ecological footprint of its operations and the exhibitions it creates.They engaged employees to generate ideas and recommendations for reducing energy consumption and waste – implementing small and large changes across the organization.
For the Planetopia exhibition, they established a goal to use 95% reused materials and devices. This required flexibility in design as they needed to find used materials that fit their needs and they experimented with unorthodox used materials choices for some design features. The team achieved 90% use of reused materials and equipment in their exhibition — just shy of their 95% goal — because some used materials proved ineffective for signage, and there wasn’t enough time to source and experiment with additional alternatives.
According to the exhibition Project Manager, Ulrich Schenk, their typical process of conception, planning, production and construction did not work as usual. They needed to rethink how to realise an exhibition.
While the planning and design process differed, the exhibition designer refused to let reuse of materials dictate the design. In early planning, the Project Manager proposed a shabby chic design as he thought it fit their reuse goals. Team members disagreed, strongly believing that they could achieve a design high standard irrespective of the priority to deploy reused materials.
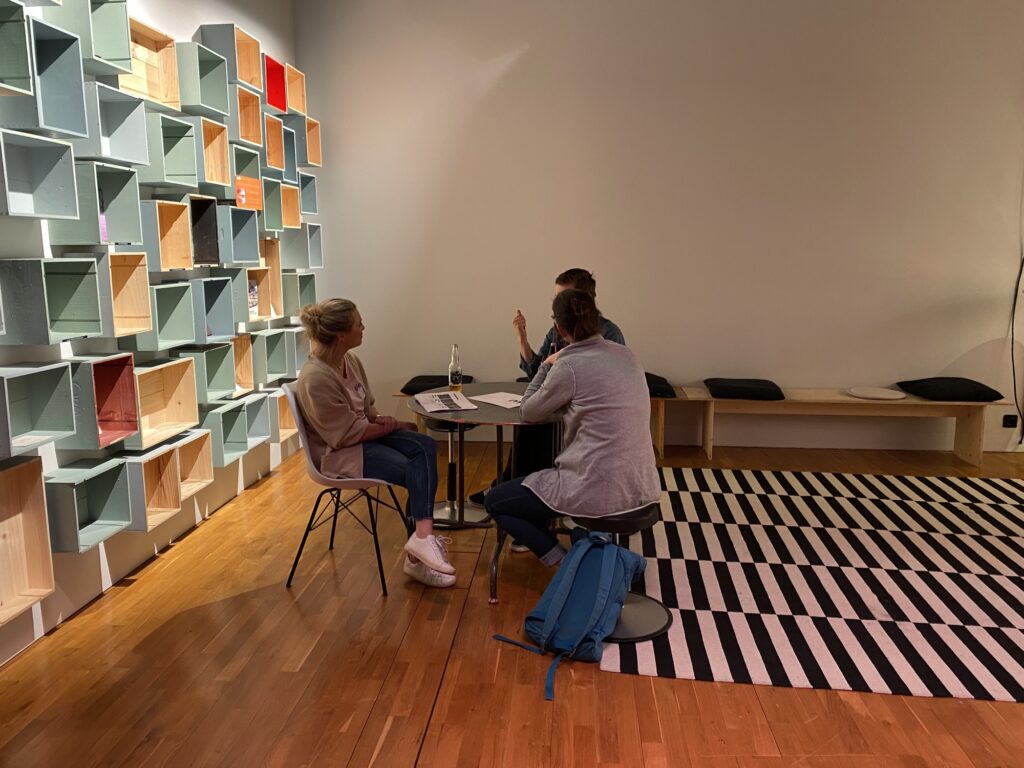
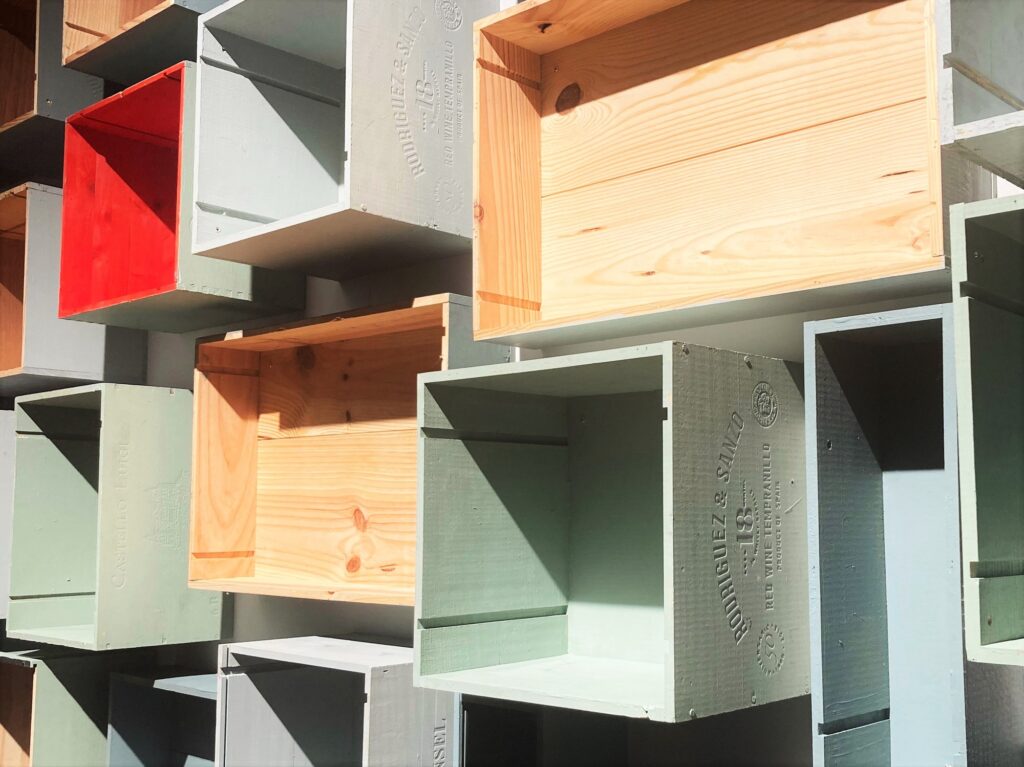
Key Learnings
1. Reusing materials can take more time than purchasing new ones if you lack a strong network for sourcing and transporting them. Additionally, the processes for acquiring and working with reused materials often differ significantly from those for new materials.
Reusing may take more time than buying new if you do not have a good network for sourcing and transporting used materials, and the procedures may differ significantly from building with new materials.
2. Sourcing used materials is unlikely to save money – especially if there is more time required for sourcing goods or additional steps required to adapt or repair used materials and equipment.
3. The planning and development process may differ. After conception, there is a step required to find, collect, store, and repair, and/or adapt the used materials to fit design specifications. Take this into account in scheduling and budgeting.
4. In addition to the team’s commitment to circularity, a good network for sourcing and repairing or refurbishing used goods will aid success. Visit the Exchange Hub for some opportunities for source used materials.
Source: video presentation: Planetopia: Museum for World Change, Museum of Communication in Bern, Switzerland, Green Museums Summit, 2024.